10 Tips for Selecting a Warehouse Management System
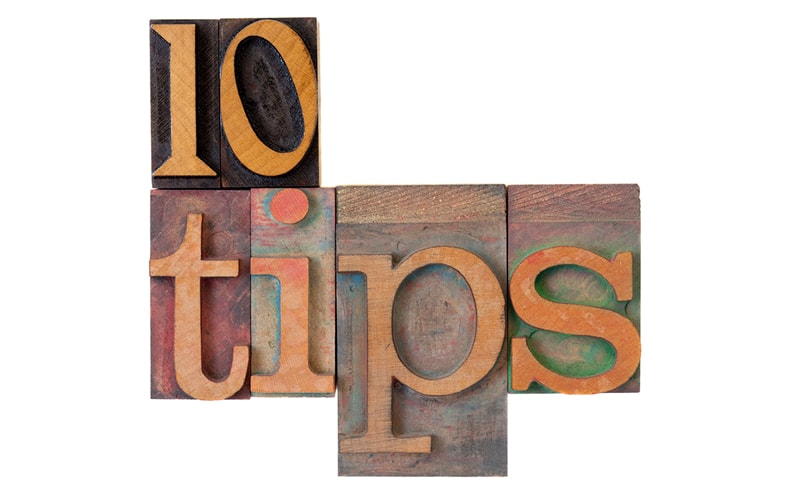
Companies must understand some important considerations to ensure they select the best warehouse management system (WMS) for their needs today and the future. These 10 steps can help focus your decision.
1. Determine operational complexity and stratify the warehouse network. Every warehouse is unique and can vary in complexity and sophistication, even within the same company across different warehouse sites. Understanding your warehouse network and the levels of complexity by warehouse helps when identifying the right WMS.
2. Understand the current state. Take stock of current operations. Are processes manual and paper-based or supported by legacy systems that might be functionally robust but aging and technically obsolete? This will influence whether you should simplify or select an advanced system.
3. Get familiar with existing applications. If you have an existing WMS (or multiple), familiarize yourself with the vendor(s) and determine if they have newer systems that you could adopt. Also, an ERP with WMS capabilities might be another route to explore if and where it makes sense.
4. Identify functional essentials. WMS is mature with parity but not equality across WMS offerings. Companies must identify the typically small number of non-standard or differentiating capabilities they absolutely must have, or the system will not work for them. These are not basic features and functions that might show up in an RFP. These are “must haves” that may require customization.
5. Map end-to-end processes. WMS solutions are good at handling the processes that take place inside a warehouse, but sometimes companies have processes that extend into other areas like manufacturing or omnichannel fulfillment. Understanding the extended process flow and integration needs is critical to success.
6. Consider business projections. A WMS has a long life span. Looking at short, medium, and long-term business projections into the future helps ensure scalability to support the business long term. Under-invest and you could be back looking at a new WMS in a few years. Buy too much and you will under-utilize the system, sometimes for decades.
7. Determine level and types of automation. Consider current and future automation needs and how the WMS will support and integrate with them. Historically, this was easier as material automation was often a significant investment and the cost helped dictate the strategy. Now, with flexible automation like intralogistics smart robots, just about any warehouse could consider automation.
8. Gauge employee readiness. Labor, both operational and IT, is a major challenge for warehouse operations. Evaluate the current composition of your team to ensure the right balance in both the business and technical aspects of deploying a new WMS. Few, if any, companies buy WMS to slash labor, but rather to improve productivity and reduce workforce churn. Aspects like user experience, flexibility, and new ways of working can lead to a more engaged workforce and should be highly rated criteria.
9. Identify improvement opportunities (ROI). It can be notoriously hard to justify the cost after installing a WMS for the first time. Companies must find additional business value for the system, such as labor management, slotting, warehouse redesign or automation. The key is identifying these opportunities and then demonstrating both hard and soft benefits to leadership.
10. Put a sharp eye to budget and financial constraints (TCO). Be brutally honest about financial constraints that could slow or stop an evaluation. Mandating a payback in less than two years might make justifying a new or replacement WMS difficult. The good news is since most WMS purchases are now cloud and SaaS-based, OPEX (an expense that is incurred through normal business operations) can help with capital appropriation. But total cost should be evaluated in both scenarios.
SOURCE: Dwight Klappich, Research Vice President and Fellow; Simon Tunstall, Director Analyst; and Federica Stufano, Sr Principal Analyst, Gartner Supply Chain Practice