Cross Docking: Definition, History, and Process
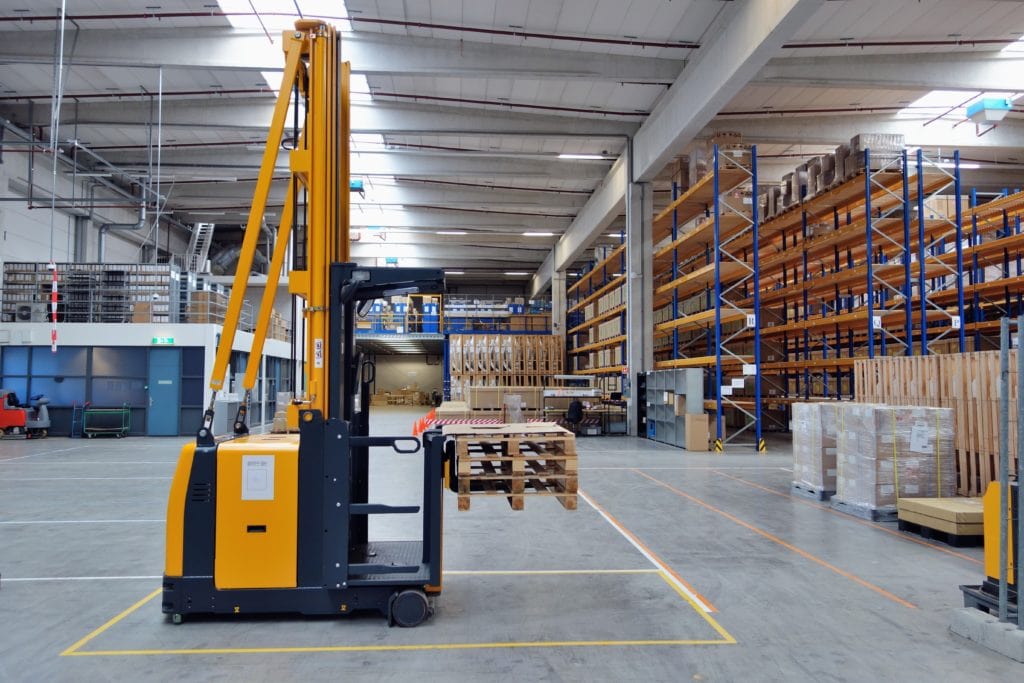
Cross docking is a shipping method that transfers goods from one transportation mode to another to get them directly from the source to their destination. Cross docking is widely used in freight transportation because it helps reduce costs and storage space, among other benefits.
This article covers cross docking definitions, history, types, methods, advantages, disadvantages, and the industries that maximize the use of the cross docking process.
What is Cross Docking?
Crossdocking involves transferring cargo or goods directly from the inbound transportation mode to the outbound one. Cross docking takes place in a distribution dock terminal where transport vehicles have dock doors on the sides and minimal storage space.
Cross docking services aim to reduce costs associated with transportation, warehousing, and storage. Cross docking also reduces the time spent transporting products by eliminating unnecessary steps such as unloading and storing items in a warehouse facility.
Cross docking is especially useful for high-volume products and perishable goods that must be shipped immediately. The process of cross docking has benefits for retailers, suppliers, and consumers.
- Retailers benefit from increased efficiency, productivity, and lower inventory costs.
- Suppliers benefit from the reduced time between receiving an order and shipping the product out, resulting in increased revenue and profit margins.
- Consumers benefit because they receive products faster than they would have if they were shipped using traditional distribution methods.
The History of Cross Docking
Back in the 1930s, the U.S. trucking industry improved cross docking processes and operations. During that time, companies were looking for ways to increase the effectiveness of their supply chain management systems, speed the delivery of goods to consumers, and lower the cost of carrying inventory.
The implementation of the cross docking method continued in the United States into the 1950s, improving supply chains particularly in the retail sector. And in the 1980s, one of the world’s largest retailers, Walmart, introduced a cross docking system that created a significant competitive advantage.
Today, companies are still looking for ways to improve the speed and efficiency of delivering goods to customers while keeping costs as low as possible. But the difference between the early days of cross docking and today’s cross docking is that modern logistics technology can help companies ensure that goods are not lost or misplaced during the cross docking process in a cross docking facility.
Types of Cross Docking
Cross docking is an effective method that can optimize supply chain operations and increase efficiency. However, it’s essential to know the differences between the types of cross docking so you can decide which one is best for your business.
Pre-Distribution Cross Docking
Pre-distribution is the most basic type of cross docking. It processes the receiving, unloading, sorting, and repackaging of items based on a pre-established distribution instruction. When using pre-distribution cross docking, inventory items stay at the cross docking warehouse only briefly.
Pre-distribution cross docking, the customer’s information is provided to the warehouse staff even before the supplier ships the products. This cross docking type suits retailers who run their own warehouses and have complete control over all their interactions with customers and suppliers.
Post-Distribution Cross Docking
Post-distribution cross docking is a process that involves arranging and keeping items in the docking facility for a short period or until the customers are determined. It enables sellers to make more knowledgeable decisions concerning shipping, inventory, sales forecasts, and trends so they can distribute goods more effectively.
Post-distribution cross docking is well suited for distributors and retailers who carefully plan where to ship their merchandise based on various factors such as seasonality, weather conditions, and consumer preferences.
Methods of Cross Docking
Cross docking can be applied across all modes of transportation, including air freight, trucking, rail, and waterborne shipping. It is accomplished using three essential methods.
Continuous Cross Docking
Continuous cross docking is a method of cross docking where goods move in a constant flow between the receiving and shipping areas. This minimizes waiting times between the unloading and loading of cargo, which results in more efficient use of time and space at the terminal.
In this method, multiple trucks drive up to a set of doors at one side of the distribution center, unload their cargo, then reload onto another truck on the other side. Terminals will have many trucks lined up in this fashion, one after another, ready to be loaded or unloaded as needed.
Consolidation Arrangements
The consolidation arrangement method combines multiple small shipments before transportation. The items are temporarily kept in a terminal warehouse until they are shipped out of the facility in full truckloads.
Consolidation arrangements are made so that more space is available for storage. They also increase efficiency as cross docking facilities need to handle fewer shipments. Consolidation arrangements also reduce the number of shipments, which can increase customer satisfaction through lower freight costs associated with each shipment.
De-Consolidation
De-consolidation is a method of dividing large shipments into smaller batches. It is frequently applied in fulfillment for direct-to-consumer sales, where goods are delivered to customers’ homes or business locations.
With de-consolidation, businesses reduce transfer, handling, and transportation costs while customers receive their orders much more quickly. Companies employing this strategy must be sure they have sufficient compliance, auditability, and traceability.
Advantages of Cross Docking
Cross docking is an excellent way for businesses to streamline operations and ship products quickly. The following are the advantages of using the cross docking method.
Faster Shipping and Receiving
Cross docking is an excellent option for companies that ship their products to their final locations. With cross docking, products can be stored with less or no labor, which speeds delivery to the final location.
As larger volumes of products are divided into smaller shipments and loaded onto trucks traveling in the same direction, shipping efficiency also rises. This makes it easier for manufacturers and distributors to keep up with customer demand for faster delivery times.
Increase Cost Savings
Cross docks can help save money in many ways. For example, eliminating the need to store finished goods significantly reduces storage costs. Reducing the number of steps in the production process also cuts labor costs and transportation expenses for finished goods.
Additionally, cross docking helps keep inventory levels low; this reduces purchasing and carrying costs.
Reduced Time
Cross docking aims to improve supply chain efficiency by reducing the time it takes for products to move from one stage of production or distribution to another. It allows businesses to spend less time managing their inventory while maintaining proper stock levels between locations.
The ability to ship products quickly and efficiently is crucial for businesses with high-volume sales. Cross docking helps keep everything moving on schedule, so customers know they can count on getting their orders quickly.
Central Location for Product Handling
Cross docking can help centralize product handling in one location. This means that fewer people handle the product, and there’s less chance for human error.
Having last-mile distribution occur from one central location also optimizes the supply chain. This helps reduce travel time and costs associated with moving products and decreases the amount of space needed at each facility or warehouse location.
Minimal Material Handling
One of the main advantages of cross docking is that it eliminates the need for multiple transfers. As a result, there is less inventory handling and less risk of damage. In addition, storage requirements are reduced because inventory is maintained at lower levels.
Goods with a shorter shelf life or those that benefit from end users acquiring them sooner can be moved into reverse flow transportation networks more quickly than traditional processes allow.
Disadvantages of Cross Docking
The cross docking has drawbacks as well. The following are some disadvantages that cross docking may bring to a business.
Fewer Suppliers
As with many supply chain operations, cross docking is a highly automated process. Cross docking automation means that it requires less human labor to operate than other inventory management methods, making it cheaper for a company to maintain.
However, this also means that fewer suppliers are needed. Some companies have only one supplier for their cross docking operation, meaning they don’t have any choice regarding which products they can carry and how much they cost.
Supply Chain Vulnerability
The most apparent disadvantage is vulnerability to supply chain disruption. Supply chains become much more vulnerable to disruption with less inventory and shorter lead times.
The longer lead times associated with traditional warehousing are also advantageous because they allow companies to plan for disruptions and set up contingency plans if needed. With cross docking, however, there isn’t as much time for contingency planning because everything happens quickly.
Reduced Storage Availability
Another disadvantage of cross docking is the loss of control over inventory. This may mean that cross docked products are stored in areas where they are not customarily kept or outdoors on pallets. There is not as much time to keep track of this inventory because it comes and goes quickly.
As a result, there is less control over product quality, availability, and safety compared to traditional warehouses, where shipments are stored for longer periods before being loaded onto trucks or trains.
Handling Complexity
Cross docking is more complex than traditional warehousing, so it carries more risk of error. The extra steps involved in cross docking, including communicating with other warehouses and coordinating their operations, can complicate the process.
This complexity directly impacts costs as well; a company may need to hire additional staff or invest in new software to handle the extra work involved in cross docking operations.
Cross Docking Best Practices
With the increasing popularity of cross docking service, these are the best practices to consider when setting up a warehouse system.
Warehouse Shape
Your facility must be able to support the cross docking process. The shape of the warehouse should be designed to maximize space and minimize travel distance. It is also vital to have storage that has a well-organized product flow throughout the warehouse to maintain efficient performance.
Number and Placement of Dock Doors
The number and placement of dock doors are critical design considerations. Depending on the size of your warehouse, you should aim for an even distribution that can accommodate all inbound shipments. The number, size, and placement of dock doors determines how long it takes for materials to be processed through your cross docking operation.
If too many doors are too small or far apart from each other, your operation will be slow and inefficient. If there aren’t enough doors, incoming trucks get backed up with nowhere to go while they wait their turn to unload their cargo into the storage facility.
Inbound and Outbound Shipments Schedule
The number of inbound and outbound shipments should be balanced. A large number of inbound shipments causes excessive congestion at the dock, while a large number of outbound shipments leaves too much space available on the dock.
An excellent way to achieve balance is to ensure that all carriers are scheduled to arrive at consistent times throughout the day and week. Avoid having one carrier pick up more than one shipment every two hours, as this causes too much movement at once and creates delays.
Industries That Use Cross Docking
Cross-docking services are helpful in many industries, especially those that handle high volumes of material on a regular basis that need to be moved quickly. The following are the industries that benefit the most from cross docking.
Food and Beverage
One of the most common users of cross docking is the food and beverage industry. These companies regularly handle high volumes of material, which can include fragile and perishable goods.
Because they need to be able to rapidly sort, store, and distribute these materials, cross docking provides an efficient solution. Another reason this industry uses cross docking is that multiple steps are often involved before products reach their final destination.
Consumer Goods
Consumer goods companies are a great example of industries that benefit from cross docking. Most consumer goods are perishable, low-value items, meaning they’re produced and sold quickly.
That’s why some companies in this industry use cross docking to move product out the door as soon as possible after it arrives at their warehouses—it helps them avoid any potential waste or spoilage while also ensuring they can meet customer demand.
Automotive
The automotive industry is a high-volume, highly competitive industry. The number of SKUs in the automotive industry is very high, as is the level of variability in product size and weight.
All these factors are considered while designing and implementing the cross docking process.
Chemicals
The chemical industry provides an excellent example of cross docking. Chemical products are shipped in large containers and can be unloaded directly into specialized warehouses.
The cross docking process saves time and money, as it reduces the time products are exposed to the elements during transportation. It also reduces the risk of product damage that might occur if there were a problem with the transport vehicle.
Conclusion
Cross docking is a way to optimize distribution space and increase profitability. In cross docking, products are received directly from a manufacturer or supplier and placed immediately into the next step in the supply chain process. This eliminates the need for warehouses, inventory, and shipping, which reduces costs overall.
It can be used for many products, including food and beverage items. With the proper logistics solution in place, you will be able to make sure that all cross docking operations run smoothly so that you can focus on other aspects of running your business.