Logistics Solutions: Robots Step Up
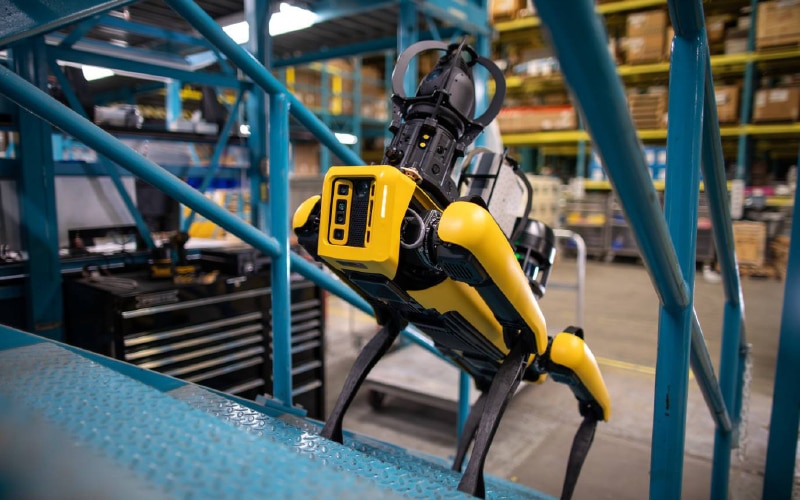
Taking on repetitive and potentially dangerous tasks in supply chain operations—from unloading containers to materials handling—robots are driving efficiencies in warehouses and distribution centers. And they’re getting smarter, thanks to AI.
PREDICTION
Artificial intelligence (AI) will drive the adoption of collaborative robots (cobots).
Revenue from collaborative robotics hardware is expected to grow 20% year over year, achieving $1 billion in 2024, according to ABI Research.
Warehouses and factories are deploying cobots, which are designed to safely work with people. Universal Robots, Techman Robot, Doosan Robotics, and ABB are some cobot suppliers that are integrating technologies like machine vision, intelligent sensors, and AI-based controls to enhance human-robot collaboration.
Advances in AI and the democratization of industrial AI development will lower barriers to reconfiguring and reprogramming cobots on the fly to meet changing production needs. Additionally, the decreasing costs of hardware like sensors, actuators, and cameras will help drive down prices and spur adoption. With improving capabilities and affordability, cobots are set for strong growth.
↑ AmbiSort B-Series: Ambi Robotics’ modular parcel induction and sorting solution for middle-mile operations automates sorting operations. It can reduce operating costs by inducting and sorting parcels into gaylord destinations. The AmbiSort B-Series solution adapts to various use cases, such as reverse logistics, inter-facility sortation, sort-to-carrier, zone-skipping, and automated parcel induction.
↑ Mecalux Robotic Order Picking System: Mecalux’s new automated solution incorporates Siemens’ SIMATIC Robot Pick AI technology, a vision software that employs deep learning algorithms to streamline picking in warehouses. With AI integrated into the programmable logic controller (SIMATIC S7-1500), the cobot performs order picking with autonomy and accuracy.
PREDICTION
Humanoid robots will likely take on one job in warehouses over the next several years.
While humanoid robots are impressive, they may not yet fulfill the needs of a warehouse environment, which is typically much more dynamic and unpredictable than the controlled settings in which the humanoid robots are performing their stunts on viral videos.
As AI and robotic technologies advance over the next several years, it is possible humanoid robots may serve a specific purpose within the warehouse. One potential use case is mobile carton picking, which has been notoriously difficult to automate.
–Brian Gaunt, VP, Accelerated Digitalization, DHL Supply Chain
• Boston Dynamics Spot and Stretch: Boston Dynamics’ Spot can operate without intervention—autonomously charging, replanning around new obstacles, and self-righting if it falls. With 360° perception, Spot offers more than 30 pounds of payload capacity and provides a sensing platform so organizations can glean insights into operations.
Stretch (pictured below) is a mobile autonomous robot that performs package handling tasks. It can handle packages of various sizes weighing up to 50 pounds and can work continuously for up to 16 hours. The robot unloads floor-loaded trucks and containers.
CEVA Logistics tapped Stretch and Spot robots to serve its customers at its new site, a 135,000-square-foot transload facility near the Port of Long Beach and the Port of Los Angeles. While Stretch robots unload hundreds of boxes per hour at the facility, Spot robots (pictured above) patrol the site and ensure security.
Meanwhile, supply chain and ecommerce service provider Arvato deployed Stretch robots (below) at its Louisville, Kentucky, logistics site, and has plans to expand their use at its global logistics centers.
PREDICTION
Generative artificial intelligence will achieve critical mass for robotics by 2028.
The robotics industry is experiencing a paradigm shift—moving from a focus on hardware to software, so there is immense opportunity for GenAI applications. While the robotics industry is historically slow-moving to adapt to new technologies due to its complexity, GenAI will be felt industry-wide within the next 5 years. When it does reach critical mass, applications for mobile robots could include more sophisticated navigation behaviors based on interactions with their environment.
–Amir Bousani, Co-founder and CEO, RGo Robotics
↑ Kassow Robots Cobots: The line of five 7-axis cobots, with a reach of up to approximately 70 inches and payloads up to 40 pounds, offers small footprints and increased maneuverability. The collaborative robots can help companies perform complex automation tasks in materials handling and other industrial applications. The seventh axis, or “wrist joint,” enables continuous dispensing, welding, and material removal, regardless of access angle.
↑ Corvus One: The flagship product of Corvus Robotics, Corvus One is an automated warehouse inventory drone solution. Powered by AI and equipped with depth perception technology, Corvus One can navigate warehouses autonomously and capture real-time inventory data, improving reporting accuracy and minimizing stock discrepancies. Corvus One is suitable for large-scale operations.
↑ Contoro Unloading Robot: The container unloading robot from Contoro Robotics automates devanning or container stripping. The autonomous robot can enter a trailer and can lift non-palletized cartons that are 8-30 inches and up to 40 pounds. Contoro Robotics charges per container with no upfront costs or equipment purchase to make the solution accessible to any sized organization.
← Hai Robotics and GreyOrange Automated Robotic Fulfillment: A partnership between Hai Robotics and GreyOrange has resulted in 10 completed robotic fulfillment projects, helping companies—including the largest retailer in the United States, one of the largest fashion retailers in the world, and other large-scale retailers across the United States and Europe—increase throughput, storage density, and agility.
GreyOrange’s fulfillment orchestration platform, GreyMatter, connects and runs both Hai’s tote-to-person autonomous mobile robots (AMRs) and GreyOrange’s rack-to-person AMRs on a single grid—unifying cross-functional operations throughout a facility for streamlined operations.
Hai Robotics’ automated storage and retrieval systems (AS/RS)—driven by autonomous case-handling mobile robots (ACR)—offer flexibility with storage density for tote, tray, box, or oversized items.
Hai’s goods-to-person systems can be constructed using almost any industry-standard racking and containers. Systems can have varying heights up to 33 feet and accommodate different container sizes and materials, stored up to 5 totes deep.
→ Geekplus RoboShuttle: The latest tote-to-person system from Geekplus supports the storage and picking of various sized items on racks, pallets, and totes within an adaptable layout. Going up to nearly 40 feet in height, its mobile AS/RS system can completely utilize a facility’s vertical space. Geekplus mobile robots are managed by a software platform that incorporates real-time path planning, traffic management, and task assignments.
↑ Dexterity Robotic Print and Apply Palletizer: Designed for retail, consumer packaged goods (CPG), and third-party logistics (3PL) operations that require case-level labeling, Dexterity’s new palletizer provides a one-robot workflow to ensure Amazon Routing, SSCC, or SKU barcodes are applied to each case in a pallet before shipment. The system identifies cases, applies labels according to customer requirements, and replicates pallet patterns. Working with a variety of pallet/conveyor input and output combinations, the palletizer can be used in inbound, storage, and outbound processes and can achieve a throughput rate of up to 300 cases per hour.
↑ Pickle Robot Unload Systems: Using GenAI, machine learning, computer vision, and sensors, the Pickle Robot solutions automate trailer and container unloading. They work with people on loading docks to make the work safer, faster, and more efficient. Under a Robotics-as-a-Service agreement, Yusen Logistics recently integrated the Pickle Robot systems at its transloading operation in Long Beach, California, which transloads around 200,000 ocean freight containers a year.
↑ Movu eligo Robot Picking Arm: The new integrated robotic bin picking solution, developed in collaboration with Righthand Robotics, can automatically piece-pick from a single-SKU source bin and place the individual items into multiple mixed-SKU destination bins. Movu eligo can pick up to 600 items per hour. The plug-and-play sub-system can integrate with the Movu escala binshuttle for an end-to-end, storage-to-picking automated solution.
↑ SCALLOG Robotic Solution: The SCALLOG solution—mobile shelves transported by robots to operators—enhances efficiency at NEWPHARMA’s logistics distribution center in Wandre, Belgium. The online pharmacy integrated the robotic goods-to-person solution into its multi-story warehouse and operational flows in 2021.
The SCALLOG solution now comprises 275 mobile shelves transported by 20 robots to four order preparation stations, including one dedicated to restocking. Covering approximately 16,100 square feet on a mezzanine, the SCALLOG zone has a small footprint. Every other NEWPHARMA order passes through the SCALLOG area, with up to 13,000 products picked each day and 24,000 products restocked.
Here Come the Humanoids
Amazon began testing a bipedal robot called Digit in fall 2023. Made by Agility Robotics, a startup firm that is funded by Amazon’s Industrial Innovation Fund, Digit is helping Amazon employees consolidate and recycle empty totes once inventory has been picked out of them.
Agility plans to mass-produce Digit robots at a facility in Salem, Oregon, aiming to produce more than 10,000 robots annually.
Other humanoids are in development. Figure AI and Boston Dynamics are testing humanoid robots in distribution centers. Meanwhile, Tesla’s Optimus Robot can sort objects autonomously as it can self-calibrate its arms and legs. Tech startup Apptronik is expected to launch humanoid robot Apollo in late 2024. Videos of the humanoid robot, which was built in partnership with NASA, show it case picking, palletizing, and unloading trailers.
Finetuning Robot Paths
To help companies optimize manufacturing processes and reduce cycle times, Realtime Robotics launched an Optimization-as-a-Service solution for industrial robots in November 2023. One month later, it partnered with HLS Engineering Group, which specializes in integrated engineering, to enhance the offering.
The combined solution lets manufacturers analyze and optimize their automation cells, improving efficiency and productivity within weeks instead of several months.
HLS’ scanning technology is utilized to virtualize a customer’s cells, collecting data and creating a digital twin of their manufacturing operations. The solution uses that information to analyze and identify any production bottlenecks. It rapidly generates and tests hundreds of thousands of potential robot paths, determining the best motion sequences based on target assignment, robot reach, and any other parameters requested by customers.
Volkswagen Commercial Vehicles in Hanover, Germany, recently used the service and reduced its cycle time by several seconds in a proof-of-concept project for electric vehicle manufacturing: a 2-robot cell that was welding car doors for a vehicle line.