Rail to the Rescue?
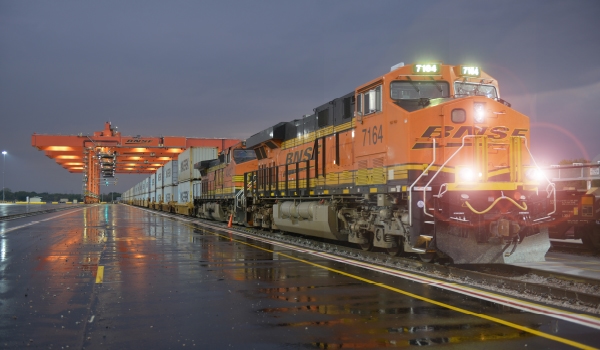
When the supply chain turns volatile and the trucking market grows tough, can these alternatives to over-the-road transportation save the day?
Over the past two years, as shippers have struggled to get loads on trucks and find affordable rates, some have started looking to the railroads for help. Intermodal rail offers a good relief valve for the highly pressured truck market. “Truck represents 94% of long-haul shipments domestically, whereas intermodal is in the 6% range, with room to grow,” says Mark McKendry, senior vice president, intermodal at NFI, a Camden, New Jersey-based third-party logistics (3PL) company.
As freight costs continue to rise, regardless of drops in oil prices, every supply chain executive is trying to pare down those expenses. “One way to cut freight costs is to consider less-expensive alternatives to truck,” notes Richard Thompson, international director, supply chain solutions at commercial real estate company Jones Lang LaSalle (JLL) in Chicago.
Intermodal also offers alternative capacity when high demand, supply chain volatility, and the ongoing driver shortage make it hard to find a long-haul truck. “Intermodal allows an organization to ship a load and not utilize a driver for the entire trip from the shipper to the consignee,” says Luke Simendinger, vice president, intermodal services at Coyote Logistics in Chicago.
In addition, shifting some volume from road to rail can help a company get closer to its environmental goals. “Depending on their freight network, the move to intermodal can reduce a company’s carbon footprint anywhere from 30 to 60%,” Simendinger says.
In the face of supply chain disruptions caused by everything from COVID lockdowns in China, to war in Ukraine, to labor disputes in North America, to natural disasters around the world, modal diversity makes a supply chain more resilient. “Companies are focused on supply chain risk mitigation,” says Thompson. “What will we do if we can’t get a truck or there’s no driver?”
Rail can offer a solution.
Reasons To Resist
In the past, many shippers avoided rail because they thought it was neither fast nor reliable enough to meet their needs. “Rail wasn’t a viable consideration for many companies, and some companies today still believe that’s the case,” Thompson says.
“Because there are more handoffs in the execution of an intermodal load—between an origin dray, a rail move, and a destination dray—there are more opportunities for exceptions in the process,” says Simendinger.
In addition to dodging a threatened strike, rail transportation poses some additional challenges.
For one, recent events have made shipping by rail more complicated and expensive. That’s partly due to the impact of Precision Scheduled Railroading (PSR), an initiative among Class I railroads to boost profits through greater efficiency.
Rail carriers have scaled back schedules, staffing, and other areas to achieve better operating ratios. Those lean operations make it hard to maintain top-quality service in the face of disruption, whether caused by hurricanes, labor shortages, or volatile consumer demand.
“Potentially, they can cut too thin,” says Ken Sherman, president of IntelliTrans, an Atlanta-based provider of logistics technology and managed supply chain services.
When demand for transportation exceeds service capacity, a railroad may limit volume by imposing a temporary embargo on some freight bound for certain locations.
For instance, from June through early September 2022, BNSF limited some westbound carload—but not intermodal—shipments into California.
“It’s complicated to manage your way around those embargoes when you ship thousands of cars per day,” says Brian Cupp, director of operations at IntelliTrans, whose rail-shipper customers use mainly carload services.
Rail shippers also face the same kind of congestion that has famously plagued ocean ports. “Congestion is not as bad at the rail terminals, but it’s still a bad situation,” says Andrew Sobko, CEO of CDL 1000, a company in Lyons, Illinois, that provides technology-based services focused on container drayage.
Not only do traffic jams in terminals increase total transit time, but they can trigger large storage fees for shippers that can’t get their containers out. “One of our largest customers recently spent $12 million on port and rail storage charges,” Sobko says.
With the right tactics, however, shippers and their third-party partners can overcome the challenges connected with rail transportation and use that mode to save money and improve operations.
A company’s best first steps are to analyze its freight, study the North American rail network, and look for places where need and capacity coincide.
“If the length of haul is greater than 750 miles, and the shipper and consignee are within 100 miles of a rail ramp, that provides good opportunities to understand what freight in the shipper’s network can be converted,” says Simendinger.
The Intermodal Association of North America (IANA)’s website offers several helpful educational resources for shippers who want to evaluate intermodal options.
Intermodal Best Practices
Here are some other best practices to consider:
Get dynamic in procuring transportation. Don’t simply assign a lane to certain carriers or a specific mode. Instead, make continuous adjustments as shipping needs, network conditions, and carrier performance fluctuate.
“Put some of that business onto the rail and start to build out a few of the capabilities within your organization,” Simendinger says. “Then work to feather that on and off, based on the service requirements of the product you’re moving in that lane.”
Route creatively. “When we see the network starting to gum up in a certain area, we make suggestions about alternative routings that might be longer in transit time, but, because of capacity issues, end up being shorter,” says Cupp.
Rail experts at IntelliTrans might also point out certain days when portions of the network are especially slow, using artificial intelligence (AI) and machine learning to spot those anomalies, he says. “For instance, we might say, ‘You should never ship to this particular location on a Thursday,’” he says.
Lose the demurrage charges. An intermodal terminal generally gives a shipper 24 to 48 hours to retrieve a container before the railroad starts applying storage charges, at $150 to $200 per container per day. CDL 1000 recently pledged to pull customers’ containers out of ocean and rail terminals within 24 hours, or else it would pay shippers’ late fees and storage costs for them.
The company has offered this guarantee to its biggest customers in the largest rail centers for some time, as long as those shippers give all their drayage business in a market to CDL 1000. Now, the company is extending that pledge to customers of all sizes. “If you fully outsource your entire market to us—let’s say in Chicago, or Memphis—we guarantee that you will pay zero in storage costs,” Sobko says.
CDL 1000 fulfills this pledge by getting containers out of terminals even when no appointments are available at destination warehouses. The company uses its own container yards to store the boxes. “We have massive infrastructure near the biggest rail terminals in the country,” Sobko says.
CDL 1000 soon plans to extend its guarantee across the entire United States by acquiring some drayage companies with a widespread terminal footprint.
Take a hybrid approach. If you need a faster transit than standard rail service provides, but don’t want to pay over-the-road freight rates, premium rail service can offer a happy medium. A premium load often rides on the same train as standard-priced loads. But a premium shipper might be allowed to drop containers at the origin terminal later than other shippers and pick up containers at the destination sooner.
Coyote Logistics used a premium service, for example, to get one customer a shorter transit time from the West Coast to Pennsylvania. Normally, Coyote would have booked an intermodal shipment to the East Coast and then drayed the container to its final destination, for a total transit time of seven or eight days. Instead, Coyote put the freight on a premium service to Chicago and then arranged for a longer dray.
“We were able to put together a six-day transit, which is just slightly longer than truck,” Simendinger says.
Maintain strong communications. Because a rail shipment takes longer and is more complicated than a truck haul, it’s especially important to keep everyone informed about mode shifts.
“Identify the stakeholders who will be involved,” suggests McKendry. “Bring challenges to the surface and talk about them. Connect your logistics partners directly with the shippers and receivers, or their customers, so they’re aware of what this modal shift can look like.” For example, if you ship product to a retail chain that imposes penalties for late deliveries, that customer needs to know how a transition to intermodal will alter the distribution schedule.
Remember the special needs of rail transport. Freight on the rails endures different stresses than a load on the highway. It’s important to block and brace loads accordingly.
While some shippers seek alternative solutions to help them temporarily in a tough environment, others might ask how to weave rail and intermodal transportation into their longer-term strategies. If so, they should include the railroads in their calculations as they decide where to site factories and/or distribution centers.
“For example, say you need x number of facilities in certain locations,” Thompson says. “You might decide to move a facility 45 miles to the west to be close to an intermodal terminal that might provide an opportunity to use that kind of service.”
It’s easier to develop a supply chain with intermodal in mind than to try to layer intermodal transportation onto an existing supply chain network.
Intermodal Marketing Companies Play A Role
Companies that want to use intermodal strategically would do well to form relationships with intermodal marketing companies. For instance, NFI and other third-party partners manage entire freight moves for shippers, reselling capacity they purchase from railroads and trucking companies. They can help shippers secure capacity for the long term.
“Intermodal is not a spot business,” McKendry says. Railroads would rather give capacity to long-term customers than to “fair weather friends,” and they would rather turn freight away than reduce their prices.
“If you ship canned foods, as an example, and you have volume, you can protect yourself by working directly through NFI with the railroads, ensuring that you have a certain amount of capacity per week,” he adds.
Shippers who want to include rail in their long-term plans can also be encouraged by the operational improvements the railroads are making to make the mode more reliable.
“As shippers think about their planning horizons, now is a good time to start utilizing some of these services,” recommends Simendinger.
One-Stop Shop for Rail Management
Shippers who want to shift volume from road to rail may find that a daunting prospect, in part because they lack a central source of information about their freight. Shippers often have to use several software solutions, plus multiple railroad websites, to get the data they need.
To make rail shipping more inviting, TransmetriQ, powered by Railinc, an Association of American Railroads subsidiary that provides rail data and messaging services to the North American freight railway industry, has been rolling out a new Rail Management System (RMS) that integrates data from a wide variety of sources in a single interface.
RMS currently includes a dashboard for tracing shipments, plus modules for issuing bills of lading and performing data analytics. In 2023, TransmetriQ will add asset management, rate management, and yard management, plus a route optimization tool that uses AI and machine learning to help choose the best way to ship a load.
“Shippers can give the RMS an origin-destination pair and ask it to provide five different ways to get a shipment there, with information about the transit time and cost of each route,” explains Danny Dever, product manager at TransmetriQ. “They can then look at transit time and cost to make informed modal decisions.”
Both carload and intermodal shippers have embraced RMS. One ocean carrier uses the tracing dashboard to keep tabs on its containers as they move through the rail network.
“We built the ocean carrier a special module in the application, called Quick Trace, which allows them to quickly pull up—with integrated data from the railroads—items such as the last free day, the pickup number, and the ETA,” Dever says.
This feature should prove helpful to intermodal shippers in general. “Hopefully, shippers will get more data, and containers can flow a little faster through the terminals,” he adds.
Intermodal Picture Improves
Total intermodal volumes fell 4.3% year-over-year in the second quarter of 2022, according to the Intermodal Association of North America’s (IANA) Intermodal Quarterly report. Domestic shipments held positive ground at 4% growth, while international containers dropped 8.4% and trailers 25.2%.
“Despite this quarter’s losses, it was an improved picture relative to the first quarter,” says Joni Casey, president and CEO of IANA. “Q2 volumes exceeded Q1 by 7.4 %.”
The seven highest-density trade corridors, which collectively handled more than 60% of total volume, were all down in Q2. The Midwest-Northwest led the losses with a 20.1% decline, followed by the South Central-Southwest at 14.5%. The Intra-Southeast, Southeast-Southwest and Midwest-Southwest dropped 7.8, 5.5 and 5.3%, respectively. The Northeast-Midwest dipped 3.1%, and the Trans-Canada corridor held losses to 2.2%.
Total intermodal marketing company (IMC) volume rose 1.3% year-over-year in Q2, with intermodal traffic down 7.4 %. Highway loads, two-thirds of total IMC volume, were up 6.3%.
Where the Rubber Meets the Railroad
Bridgestone Americas has been an intermodal user for more than 15 years, utilizing the transport mode to optimize cost and service for cross-regional and long-haul moves along its distribution network.
Bridgestone Americas is the U.S. subsidiary of Bridgestone Corporation, which develops, manufactures, and markets a wide range of Bridgestone, Firestone, and associate brand tires. Bridgestone and its subsidiaries address the needs of a broad range of tire customers, including consumers, automotive and commercial vehicle original equipment manufacturers, and users in the agricultural, forestry and mining industries.
In addition to an expansive network and an abundance of lane offerings that complement Bridgestone Americas’ freight flow needs, intermodal also provides scalable capacity, helping to ease the constraints that Bridgestone and many other shippers face in the current trucking environment.
Addressing Supply Chain Challenges
Bridgestone Americas uses nearly all transportation modes, including truck, less-than-truckload (LTL), intermodal, traditional rail, ocean, air, and parcel.
These modes must accommodate the movement of both raw materials used at production facilities and finished tire products that need to be distributed across Bridgestone Americas’ network to various customer locations. Bridgestone Americas has a heavy freight footprint across long-haul lanes, representing a significant cost and lead time to manage, and this has been an important area of focus for the company.
Bridgestone Americas’ main supply chain challenges include:
- Managing logistics costs to align with overall company expectations
- Contracting and securing transportation capacity, and overcoming localized and macro constraints
- Providing a high level of service to customers who depend on consistent, reliable delivery of tire products
Intermodal services are incorporated into Bridgestone Americas’ daily planning models to source tire products to the markets served by its plants and distribution centers. When considering conversion from highway to intermodal rail, the company factors in cost, lead time requirements, intermodal service levels and capacity. To overcome misperceptions that service levels may be sacrificed by using intermodal rail, Bridgestone Americas often provides transportation manifests to its customers and counterparts to assure them that intermodal services are consistent, reliable and able to meet the demands of inventory and on-time shipment performance.
CSX Transportation (CSXT) Intermodal works with Bridgestone Americas to convert additional freight from highway to rail by reviewing overall volume commitments in the Bridgestone Americas network and highlighting freight flows that can provide cost savings and capacity that over-the-road alternatives cannot match. This review homes in on long-haul solutions to meet Bridgestone Americas’ supply chain needs of positioning inventory within its distribution network.
The Results
In addition to reliable capacity, Bridgestone Americas experiences truck-like transit times on long-haul moves, with the same or better service measurements across modes. Further, relationships with preferred carriers and intermodal marketing companies to secure rates and capacity that meet its network requirements has driven Bridgestone Americas to use more intermodal rail over time.
When considering transportation options, Bridgestone Americas assesses what mode and provider will yield the greatest value in terms of overall cost and service performance. Using intermodal has helped the company manage its large supply chain by providing the ability to plan and secure its capacity in advance through intermodal carriers. By doing so, Bridgestone Americas can eliminate bottlenecks and delays that are often experienced in the trucking market. The company values the loyalty and experience of its carriers and sustains relationships that are mutually beneficial for their business and for the selected carrier.
Bridgestone Americas considers intermodal options to be more service competitive with truckload alternatives due to improvements in rail transit times and growing hours of service constraints, which limit over-the-road drivers. In addition, Bridgestone Americas experiences savings in fuel costs for long distance moves when it uses intermodal rail.
The company’s intermodal journey has evolved over many years into a core component of its distribution network. It continues to expand upon opportunities to utilize intermodal transportation, and relies on its partnership with CSXT Intermodal to identify additional freight suited for intermodal rail conversion.
–Source: CSX