Trends—November 2015
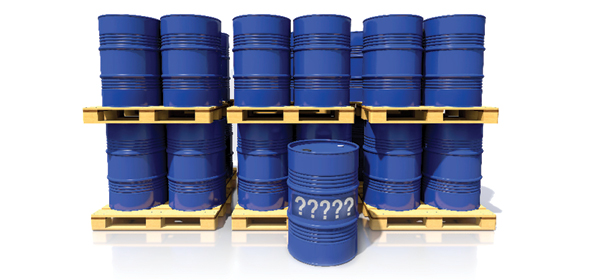
GHS: Label It a Problem
Fewer than 50 percent of the nearly 150 supply chain professionals from internationally based chemical companies responding to Loftware Inc.’s recent GHS Readiness Survey have met the latest Globally Harmonized System of Classification (GHS) labeling requirements. The United Nations originally adopted the GHS in 2002 to ensure hazardous materials are safely produced, used, and disposed of.
In addition to not using proper labeling solutions, many companies lack a barcode labeling strategy, leading to fines and potential business disruptions, according to Loftware’s survey. To avoid future fines, supply chain professionals in the chemical industry will need to adapt Enterprise Labeling Solutions that enable them to meet regulations, even as they consistently evolve.
“With GHS, companies face more regulations in chemical labeling than ever before,” says Deborah Grant, industry manager at Portsmouth, N.H.-based Loftware. “To accommodate this new level of complexity, today’s labeling must be both dynamic and data-driven to maximize flexibility, ensure accuracy without replication of data, and provide speed and scalability to meet GHS labeling standards.”
Nearly 35 percent of survey respondents acknowledge that regulatory compliance is currently the most difficult aspect of labeling. Consequently, they are interested not only in meeting labeling requirements such as barcodes, formats, and logos, but also improving the efficiency of their supply chains, which, like GHS requirements, are constantly evolving.
“Companies are recognizing the integral part that labeling plays in gaining true supply chain efficiency, achieving higher levels of customer satisfaction, maintaining business continuity, and meeting regulatory demands,” notes Josh Roffman, vice president of product management at Loftware.
“Labeling solutions must be designed to meet the rigors of GHS labeling, while supporting large-scale, global deployments with numerous products and packaging variations,” he adds.
St. Louis: Mecca For All Modes
St. Louis, Mo., remains an epicenter for all modes of transportation, which makes it ripe for future growth opportunities, according to the recent Southwestern Illinois Freight Transportation Study, overseen and released by the Leadership Council Southwestern Illinois.
The study finds that the St. Louis area’s freight capabilities will increase in the coming months and years, primarily due to the area’s domestic trade partners and economic expansion.
The study, which was funded through an Illinois Department of Transportation grant to the Leadership Council, and administered by Madison County, Ill., also projects that rail, truck, and intermodal shipments will rise as well; however, rail shipments will grow at a slower pace than truck or intermodal shipments.
Outbound freight is anticipated to increase faster than inbound shipments because the area currently produces more outbound intermodal freight than inbound intermodal cargo.
Meanwhile, the St. Louis area anticipates more than $700 million in bridge, port, rail, and roadway investments over the next five years—funds that will follow the $100 million that was already spent on bridge and roadway repairs in Madison and St. Clair counties.
“The study was primarily undertaken to determine the best ways to advance the St. Louis region as a premier multimodal hub, based on anticipated growth in the freight industry,” says Mark Harms, chair of the council’s transportation enhancement committee.
“The findings will help us better understand how certain advantages position our region in a highly competitive freight marketplace, while also identifying opportunities to build on those advantages in the future,” he adds.
3PL CEOs See Future Growth
For nearly six years, large-scale acquisitions were few and far between within the third-party logistics (3PL) industry, due to the aftermath of 2008’s global recession. Recent months have shown signs of continuous economic recovery, however. In that time, 10 major 3PL acquisitions comprising $18 billion have occurred.
As a result, 3PL CEOs are once again gaining confidence in the industry’s growth potential, reveal the 22nd Annual Surveys of Third-Party Logistics Provider CEOs, sponsored by Penske Logistics, Reading, Pa.
Of the 30 3PLs surveyed in North America, Asia Pacific, and Europe, 80 percent report profit gains in 2014. In fact, the 30 companies’ total revenue exceeded $40 billion. North American CEOs project their companies’ revenues will increase by 7.86 percent, on average, over the next three years; 6.54 percent of which will originate from merger and acquisition activity as the industry restructures considerably in a variety of markets.
3PL CEOs are also focused on e-commerce. Currently, e-commerce comprises 11.9 percent of North American 3PL revenues, and CEOs anticipate this aggregate will rise to nearly 21 percent by 2019.
North American CEOs cite two other issues affecting the industry: oil prices and the driver shortage. Eighty percent of surveyed CEOs say the oil price decline is positively influencing customers. But the driver shortage is hindering the industry; 26 percent of CEO respondents say the shortages continue to impact 3PLs throughout the world.
“The driver shortage is here, is real, and is not going away,” says Joe Carlier, senior vice president of global sales at Penske Logistics. “The global projections included in the surveys mirror our business climate. E-commerce is having an effect on our customers and many verticals are focusing on omni-channel.”
“The 3PL industry is clearly in a consolidation phase,” adds survey author Dr. Robert Lieb, professor of supply chain management at Northeastern University’s D’Amore-McKim School of Business. “And it will fundamentally change the competitive dynamics in many markets for logistics services around the world.”
SCM Tool Purchases Perk Up
Supply chain management (SCM) software tool expenditures remain a priority for logistics decision-makers, and companies intend to spend 14 percent more on SCM tools in 2016 than they did in 2015, according to Boston-based Nucleus Research’s 2016 Buying Intentions Survey.
Of the 72 supply chain leaders in North America and Europe responding to the survey, 55 percent will purchase more supply chain applications in 2016 than they did this year; while another 37 percent plan to retain their software expenditures so that they do not exceed 2015’s aggregate.
Respondents also reveal their two top choices for software investment next year: supply chain planning and inventory optimization.
“Such SCM spending is driven by a number of trends, including concerns about having a steady product supply in a volatile global, digital marketplace,” explains James Cooke, principal analyst, Nucleus Research. “And with corporate pressure to control costs in activities such as warehousing and inventory, supply chain managers continue to upgrade their execution and planning applications.”
To cut costs, nearly 25 percent of survey respondents say they would use their expenditures to continuously roll out applications they purchased in 2015, or to upgrade applications they have already used in the past.
The survey also finds that only 47 percent of the polled companies use cloud applications for software deployment. And, of the companies using a cloud application for supply chain tools, they often use only one type of application—transportation management, a trend that Nucleus Research anticipates will change in the future.
“Over the next five years, as more trading partners work together in the global marketplace, multinational corporations should become more inclined to adopt the cloud for advanced supply chain solutions to facilitate data exchange,” Cooke says.