Sites of the Stars
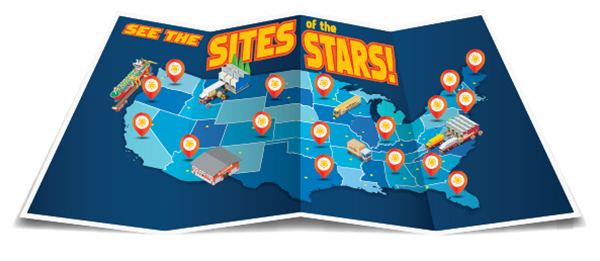
These logistics sites reach for the stars and deliver stellar performance.
Logistics site professionals play an important role. They constantly pursue new ways to move products quickly, efficiently, and safely. They know that in order to earn top billing, their methods must change in tandem with market and technology shifts. What works today may work tomorrow, but in all likelihood there is something new under the sun and something even better over the horizon.
To be leading performers, site selectors look for stellar logistics locations and services that will facilitate their journey. Which locations and services make the A-list? Who is setting the standard and who is raising it? How are they doing it? Most importantly, what can we learn from them?
The lessons the site leaders teach us—about state-of-the-art intermodal, warehousing, and distribution services—are born of both experience and vision.
Breakout Performance
When determining the best spot to locate a distribution or manufacturing facility, what makes a site stand out?
In addition to strategic location, site managers should base such decisions on the region’s business-friendly environment, labor availability, infrastructure, and land inventory, says Steve Schnur, chief operating officer, Duke Realty, a leading owner, developer, and manager of logistics real estate. Based in Indianapolis, Duke Realty’s varied markets include Atlanta, Central Florida, Chicago, Cincinnati, Columbus, Dallas, Houston, Indianapolis, Minneapolis-St. Paul, Nashville, New Jersey, Northern California, Pennsylvania, Raleigh, Savannah, Seattle, South Florida, Southern California, St. Louis, and Washington, D.C./Baltimore.
"In selecting sites for development projects, Duke Realty is extremely analytical, delving into the characteristics of specific submarkets," Schnur says. In many larger markets, Duke Realty may operate in only a few submarkets.
"In each of these submarkets, our properties are well-served by key highway networks and, in many cases, supplemented by other forms of transportation including air, rail, and sea," Schnur says. "Our facilities also are in close proximity to major population centers. From our properties, companies can easily and quickly reach their customers, whether business-to-business or the end consumer."
One of the most impactful factors that allows Duke Realty to capitalize on regional logistics assets is the local operating teams the company has in place in each of its markets. "Having boots on the ground gives us intimate knowledge of market dynamics and our customers’ needs," Schnur explains.
The company’s portfolio includes 158 million square feet of space in its 20 major logistics markets. Duke Realty is a full-service commercial real estate company, providing a wide spectrum of services, including working closely with customers on site selection, construction, financing, leasing, property management, and renewal. "By owning the land, using our in-house construction team, and leasing and managing our own properties, Duke Realty is able to provide a seamless delivery system, control costs, and manage risk," Schnur says.
Dynamic growth in the logistics sector has prompted new ideas and innovations. "Though much of the growth can be attributed to general economic expansion, there is no doubt that e-commerce has been a big piece of the equation," Schnur says. "That being said, many of our customers are challenged with delivering goods to customers faster and more efficiently than ever. Increased delivery expectations have led to using technology to better manage inventory and improve facility operations."
In turn, the new facilities being built and designed to create stellar logistics sites are focused on efficient inventory flow, including materials handling automation, product stacking and retrieval, increased dock capacity, power expansion capabilities, security, site layout, parking, and ingress/egress.
"Energy and water efficiency are also important considerations," he adds. "We increasingly incorporate features that reduce resource consumption such as increased glass lines, skylights, and dock door windows for heightened natural light, as well as LED lighting, solar panels, water-saving fixtures, EV charging stations, and efficient HVAC systems."
In addition, tenants are focused on their ability to adapt to ever-evolving logistics needs. The truly stellar site, then, incorporates flexibility and expansion capability in its design.
Top Billing
Having a strategic location as the hub of a company’s logistics operations is a major theme of any story involving stellar logistics sites. This fact is clearly evidenced by the success of Watson Land Company, a developer, owner, and manager of industrial properties throughout Southern California and the East Coast.
Watson’s legacy of success has become well established over nearly two centuries, due in large part to the strategic advantages intrinsic to the locations of its properties. The company’s expanding portfolio of properties now contains close to 20 million square feet of industrial space, affording logistics providers an array of options for their next distribution center, warehouse, or company headquarters.
Watson delivers functional, high-quality buildings within master-planned centers. Its history is rooted in the Rancho San Pedro, the first piece of land granted to a private citizen in Southern California. The property eventually evolved into Watson Estate Company, founded in 1912, and was later renamed Watson Land Company.
Developing a New Role
For more than 50 years, the land owned by the company was used for agriculture and oil production. But in response to Southern California’s rapidly changing business landscape, Watson Land Company shifted its focus to real estate development. Its goal was to enhance the value of its holdings by creating master-planned centers for industrial buildings.
In the 1960s, the master-planned Watson Industrial Center in Carson, California, where the company is based, would pave the way for the firm’s further evolution into one of the region’s most influential real estate companies, serving a broad range of regional, national, and international clients.
Watson customers enhance their location advantages—and significantly reduce their operating costs—through the activation of Foreign Trade Zone (FTZ) status. Granted through the Port of Los Angeles within the Watson subzone of FTZ 202, the FTZ status can be activated for some 12 million square feet of Watson facilities.
Companies can use the FTZ status to reduce operating costs for their manufacturing and inventory facilities. The non-privileged foreign position allows the duty rate for goods entering into an FTZ to be assessed according to the condition of the merchandise.
In addition, with access to product for display or exhibition purposes without customs intervention or supervision, utilizing an FTZ can significantly minimize bureaucratic regulations.
The FTZ designation also offers operational benefits, which companies can use to gain a competitive edge in their market. Companies have better inventory control with lower customs supervision. And the duty payable on FTZ goods doesn’t need to be included in the calculation of insurable value, which lowers insurance costs. The FTZ may be utilized to examine product so it meets accurate specifications before duty is paid.
Merchandise not meeting the requirements can then be repaired, re-exported, or destroyed without having to make duty payments. Furthermore, goods may be stored in an FTZ for unlimited periods, even if they are subject to U.S. quota constraints.
Certain types of merchandise can be imported without going through formal customs entry procedures or paying import duties until the products are transferred from the FTZ sites for U.S. consumption. If the products never enter U.S. commerce or are re-exported to other countries, duties do not need to be paid on those items.
Watson’s strategic location advantages are not limited to Southern California. In 2016, the company acquired two distribution buildings in the West Hills Business Center in Lehigh Valley, Pennsylvania, which is located on the I-78 corridor. Watson’s East Coast expansion totals 678,000 square feet of space.
Making it to the A-list
While "location, location, location" still describes the most important element in real estate, logistics professionals know it doesn’t amount to anything if property owners and tenants do not make the most of the particular spots they claim as their own. CenterPoint Properties, which invests primarily in real estate used for intermodal freight transport, knows the lesson well.
The company, which began its industrial real estate operations in 1984, invests in the coastal and inland port markets that anchor North America’s most important freight lanes. With headquarters in Oak Brook, Illinois, CenterPoint has offices in Los Angeles, Oakland, Houston, New Jersey, and Miami. The company owns 326 buildings containing 61.3 million square feet, including the CenterPoint Intermodal Center in Joliet/Elwood, Illinois, and SoCal Logistics Center in Buena Park, California.
The company’s success is built on choosing the right place at the right time, and then capitalizing on its property selections by enhancing natural logistics assets with the ultimate tenant in mind. "In its simplest form, I like to say we develop Class A and we buy Class B for functionality in the port markets," says Ryan Dunlap, senior vice president, investments, West Coast. "Not a lot of groups can do that."
Dunlap, who has been part of the CenterPoint team for three years, works out of the company’s Los Angeles office. "As the logistics sector becomes increasingly nuanced, it becomes more about the functionality of the asset," he says. "What kind of tenants need clear height? Who requires quick inventory turnover, which translates into bigger yards?"
It is the dissection of these concerns and others that spells the difference between success and failure. The key is recognizing those concerns and responding with practical solutions. "You see a lot of sophisticated premium spaces that are not functional," Dunlap explains, adding that CenterPoint reliably delivers forward-thinking solutions matched to its tenants’ development, acquisition, and management needs.
Going Places
If the three most important words in logistics are location, location, location, the three next most important words are mobility, mobility, and mobility. Put another way: It’s not just where you are, but where you are going.
The definition of a stellar logistics site, then, has everything to do with the feasibility and services it provides. CN, headquartered in Montreal, Quebec, understands that well. The Class I freight railway serves Canada and the midwestern and southern United States.
CN, "North America’s Railway," services an area encompassing more than 20,000 miles. It has the only rail network that touches three coasts in North America, accessing the Atlantic, Pacific, and Gulf coasts.
As Canada’s only transcontinental railway company, CN offers integrated transportation services including rail, intermodal, trucking, freight forwarding, warehousing, and distribution. Its rail network serves all major Canadian cities and ports as well as the U.S. metropolitan areas of Duluth, Minnesota; Superior, Wisconsin; New Orleans; Mobile, Alabama; Chicago; Memphis, Tennessee; Detroit; and Jackson, Mississippi, with connections to all points in North America.
CN moves overseas container traffic to the U.S. Midwest from the Canadian ports of Vancouver and Prince Rupert B.C.; Montreal, Quebec; and Halifax, NS.
CN services 15 ocean terminals and well over 23 strategically located intermodal terminals across its network. The company’s five logistics parks—in Calgary, Montreal, Toronto, Chicago, and Memphis—are designed for quicker transit times, efficiency, and superior rail service. Co-location of the parks within CN intermodal yards eliminates one truck move. Moreover, each site is easily reached by North America’s largest highways and puts access to all key logistics services—rail, intermodal, warehousing, and distribution—in one place. Easily accessed by North America’s largest highways, CN’s logistics parks are modern, state-of-the-art facilities with dedicated teams to handle cargo.
CN transports more than $250 billion Canadian worth of goods annually for a wide range of business sectors, from resource products to manufactured products to consumer goods.
On the rise
Like the many tons of cargo it handles, CN is constantly on the move. Among recent expansions is the company’s new intermodal terminal opening later this fall in Regina. The terminal will connect southern Saskatchewan to global markets and offers an intermodal option for shippers from North Dakota and Montana to get their products to West Coast ports for trans-Pacific shipping. The facility is the first privately operated, state-of-the-art intermodal terminal and is located in the Chuka Creek Business Park.
Meanwhile, CN recently announced two new agreements with COSCO and Evergreen shipping lines, extending their longstanding intermodal partnerships.
These recent announcements are the product of CN’s focus on strategic and profitable growth in the intermodal sector as CN remains committed to offering the best intermodal rail service in North America.
In September, CN announced that it again has earned a place on the Dow Jones Sustainability World Index (DJSI). This marks the eighth consecutive year that CN has been listed on the DJSI World Index and the 11th consecutive year that CN has been listed on the DJSI North America Index. CN is the only Canadian company listed in the Transportation and Transportation Infrastructure sector.
The DJSI tracks the performance of the top 10% of the 2,500 largest companies in the S&P Global Broad Market Index that lead the field in terms of sustainability. The DJSI follows a best-in-class approach, surveying sustainability leaders from each industry on a global and regional level. The annual review of the DJSI family is based on a thorough analysis of economic, environmental, and social performance, assessing issues such as corporate governance, risk management, climate change mitigation, supply chain standards, stakeholder engagement, and labor practices.
"We are honored that CN’s sustainability performance continues to earn us a place among the world’s best," said JJ Ruest, president and chief executive officer of CN. "2019 marks CN’s 100th anniversary and we have a great deal to be proud of. As we move into our next century, we renew our commitment to be a leader in safety, sustainability, innovation, and growth."
Playing a Pivotal Part
In the end, for a logistics site to be stellar, it all comes down to proximity. In logistics, the word means more than just nearness in space and time, though those advantages are surely vital. Even more important are the synergies achieved through the locations of intermodal facilities and supply chain services.
A prominent case in point, and certainly qualifying the region as a stellar logistics site, is the area served by the North Carolina State Ports Authority, otherwise known as North Carolina Ports. As a congestion-free mid-Atlantic gateway, North Carolina Ports provides immediate proximity advantages for supply chains in the region.
North Carolina is home to two ports. The Port of Wilmington services containers and general cargo, while the Port of Morehead City handles general cargo—bulk and breakbulk. Both ports are mileage favorable to all North Carolina metropolitan areas—the Greater Charlotte region, Piedmont Triad, Research Triangle, Greater Fayetteville, and the southern and eastern coasts.
Supporting Turn
"Our best-in-class yard and gate productivity, fast truck turnaround times, crane productivity, and lack of berth congestion make North Carolina Ports a logical choice for speed to market for all industry sectors in North Carolina," says Hans Bean, senior vice president of business development for North Carolina Ports.
"Our average turn time for truckers is a best-in-class 32 minutes for a dual move," he adds. "With this consistent best-in-class port performance, we are seeing importers attracted to the area to achieve necessary flow velocity, gateway diversification, and risk-mitigation objectives."
In addition to its proximity and performance advantages, Bean says, area exporters also appreciate the user-friendly nature of North Carolina Ports in supporting their business requirements.
"Our ability to be nimble, combined with our out-of-the box thinking, allows us to serve all industry segments in North Carolina and beyond," he says. "For many of the area’s core industry segments, North Carolina Ports is the closest to source/production and to market/distribution."
Coupled with recent infrastructure upgrades and a vision for serving the future, he says, these proximity advantages have positioned North Carolina Ports well to deliver value across supply chains.
In 2015, North Carolina Ports developed a five-year strategic plan that included capital investment for future growth. The authority committed more than $200 million for a new terminal operating system, gate and terminal operations reconfiguration, three neo-Panamax cranes, and turning basin enhancements.
Additionally, on-dock rail service was revitalized in 2017, linking the Port of Wilmington to the western part of the state including eastern Tennessee, northwest South Carolina, southwest Virginia, and southeastern Kentucky.
The overnight rail service operates seven days a week between Wilmington and the Charlotte Inland Port. This reduces carbon footprint as well as truck miles in the western area and provides the fastest rail service inland on the East Coast.
North Carolina Ports continues to invest in refrigerated capability to serve as a cold chain gateway for imports of produce that complement the region’s significant refrigerated agricultural exports. The authority has commenced construction on an investment of more than $15 million in a refrigerated container capacity expansion with vertical racks that increase fixed plug capacity from 350 to 550, with phase two adding approximately 300 additional plugs and further room to expand to serve the market.
"We are strategically investigating partnerships with refrigerated warehouse operators that would enhance our cold capabilities to support the North Carolina grocery sector and beyond," Bean says.
"We are also continuing to look at alternatives to the growing agricultural segment of North Carolina as well as provide another East Coast gateway for Midwest agriculture products. These alternatives include an on-dock transload facility that can be both rail and truck served."
Red Carpet Treatment
North Carolina Ports partners with local and regional trucking companies as well as local and regional warehouses, Bean says, adding that there are multiple megasites available in North Carolina for future expansion. He says the authority is consistently working with its economic development partners to attract business to those sites.
North Carolina Ports offers on-dock rail just a few hundred feet from vessel berths. Inland connectivity with Norfolk Southern and CSX includes legacy tracks that can be further networked for optimized services, and inland ports near rail ramps offer flexible staging and access options.
"In today’s environment it is all about visibility, speed, and cost containment," Bean says. "North Carolina Ports will continue to be the best on the East Coast for port productivity. We will invest in technology that will allow us to proactively push information not only to the end customer, but also to the freight forwarding and trucking communities, allowing for operational process improvement and informed operational decision making."
Not surprisingly, all these factors fit into logistics site professionals’ definition of a stellar logistics site.