The Georgia Connection(s)
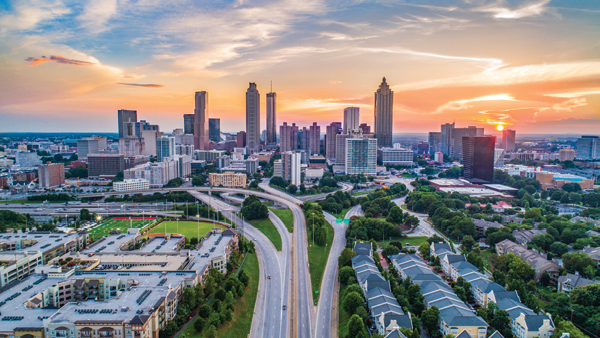
The essence of logistics is making connections. No surprise, then, that Georgia—a state where connectivity is a way of life—is a shining star on the logistics land (and air and sea) scape.
Ask Pat Wilson, commissioner of the Georgia Department of Economic Development (GDEcD), to explain why his state repeatedly is cited as an American logistics superstar, and be prepared to hear—among the litany of obvious logistics assets including location, ports, roads, airports, education, workforce, and business climate—the one element that literally puts it all together: connections.
Logistics thrives in Georgia, Wilson says, because leaders have long understood that logistics is the art and science of making connections. Under the leadership of Gov. Brian Kemp, Wilson’s department is charged with the responsibility of linking the state’s assets to form what Wilson describes as a “logistics juggernaut.”
In addition to the state’s geographic, economic, education, and infrastructure advantages, the most vital links in the supply chain are Georgians themselves. Wilson tells the story of a CEO who made a site-selection visit to the state. After deciding to locate in Georgia, the CEO said what impressed him most was the familiarity business and political leaders had with one another.
“Everybody in that room knew each other,” Wilson quotes the CEO as saying after meeting with business and government leaders. It was, the executive said, an experience unlike any other.
Site-selection experts often teach the lesson: In order for a location to attract business, it first must be somewhere that people want to live. For both business and pleasure, that requires great schools, great services, and an environment of hospitality, cooperation, and mutual support.
It all comes down to connections. And in Georgia, those connections often begin at the GDEcD. “One of the things we pride ourselves on is being a one-stop shop for companies,” Wilson says. “We are the connection. We help leverage all the resources. That’s our place in the model.”
“All the resources” include technical colleges, universities, and local partners such as utilities, in addition to the state’s ports, airports, rail lines, roads, and highways.
The GDEcD’s Global Commerce team focuses on helping companies of all sizes, industries and regions—from Georgia and from across the globe—make the connections they need to ensure their businesses flourish in the Peach State.
Rapid Response
To achieve that goal, external problems must be dealt with promptly and effectively. In March 2020, for example, Gov. Kemp called on businesses to assist in providing necessary medical resources in the wake of the pandemic.
The Global Commerce team continues to help Wilson’s department spearhead this effort along with the department’s Center of Innovation by connecting with manufacturers, small businesses, and innovators from across the state to produce, store, and distribute critical healthcare supplies.
“The response that our team has received from our partners has been remarkable,” Wilson says. Across responsibilities—including international trade—the GDEcD team has helped companies pivot from their original strategies, source raw materials for their retooled production, and navigate new protocols for health, safety, and sustainability.
Locales as diverse as China, Brazil, and Canada have provided direct aid and support while continuing to work with the state government to keep their Georgia-based employees safe and productive.
The Center’s specialty is drilling down to the details and linking new and expanding businesses to staff experts and external partners and to independent mentors who can help spark inspired solutions for challenges and opportunities of any size.
The Center identifies “touch points” for businesses, including private sector partners, says Wilson. All services are free of charge. The Center’s logistics team helps companies improve supply chain efficiencies, support growth, and increase global competitiveness. It connects companies to the technical industry expertise, collaborative research, and partnerships that cargo-owning companies need.
Long-term Support
Not only does the state government pride itself on recruiting businesses to Georgia and providing assistance in times of urgent need, but it also is structured to provide long-term support “once a company lands in Georgia,” Wilson says.
“If you are employing Georgians, we are going to work with you as you continue to grow,” he says. “You have become part of the Georgia family of companies.”
That ongoing sense of community and partnership is “truly a differentiator for the state,” he says. “That’s what sets Georgia apart.” Georgia seeks to be a place where people want to “live, work, play, and enjoy their lives,” he adds.
“For 150 years, the reason the economy has boomed in Georgia is logistics,” Wilson says. “Throughout our history, we’ve had governors and General Assemblies that have made investment in logistics a priority.”
The state’s logistics assets reflect these efforts:
- Two international airports—Hartsfield-Jackson Atlanta and Savannah/Hilton Head—and nine of the top 10 cargo airlines in the world.
- Both of the Eastern U.S. Class I railroads, CSX and Norfolk Southern, along with 24 short-line railroads.
- Two deep-water ports, Savannah—the fastest-growing port in the United States—and Brunswick.
- Six U.S. interstates—1,200 miles of highway—connecting shippers to 80% of the country in two days or less driving time.
Superior Ports
Prominent among Georgia’s logistics assets is the Georgia Ports Authority (GPA), a major driver of jobs and business opportunities in the state. Georgia’s deepwater ports and inland barge terminals support some 500,000 jobs and contribute $29 billion in income annually in Georgia. The ports generate $122 billion in revenue and $3.4 billion in state and local taxes.
The Port of Savannah handled 9.3% of total U.S. containerized cargo volume and 10.5% of all U.S. containerized exports in the 2020 fiscal year, GPA reports. Behind those numbers is an impressive record of service.
“GPA provides greater scheduling flexibility and market reach through Savannah, with 35 weekly containership services, direct interstate connections, and on-terminal rail,” explains GPA Executive Director Griff Lynch. “Intermodal service is provided by Class I railroads CSX and Norfolk Southern.
“The Port of Savannah is closest and fastest by rail to the major population centers of Atlanta, Memphis, Nashville, Charlotte, Huntsville, and Birmingham,” he adds. “On-terminal service from two Class I railroads means more schedule and routing choices.”
A major expansion project, the Mason Mega Rail Terminal, has increased the Port of Savannah’s rail lift capacity to 2 million TEUs per year, Lynch reports.
As the most westerly major container port on the U.S. East Coast, Savannah is poised to take advantage of its broad global shipping network and enhanced rail capacity to provide expanded intermodal service to major inland markets. This stronger rail link will provide customers a new opportunity to take advantage of Savannah’s timely, reliable terminal services.
Additionally, the Port of Savannah enjoys superior truck connections. Immediate access to I-16 (East/West) and I-95 (North/South) means key cities and manufacturing points throughout the U.S. Southeast and Midwest may be reached within a one- to two-day drive.
Responsiveness to Change
Lynch says the increasing role of digitalization in shipping has strongly affected GPA’s approach to its work.
“Traditionally, the data used by the terminal operator is inclusive of the waterside operations, and lacking on the landside,” he says. “GPA strives to improve the sharing of data and knowledge with the landside operations to improve the flow of cargo from berth to store.
“This is a pioneering effort, not standardized, and is gaining traction every day,” Lynch adds.
For those considering moving to or expanding within Georgia, the state provides a series of job tax credits, including special enhancements for port-using industries. Additionally, there is ample land available near Georgia’s port facilities and rail hubs to ensure the efficient movement of manufacturing components and finished goods.
Lynch describes the state’s Quick Start program, which provides targeted workforce training, as a national model. Quick Start develops and delivers fully customized, strategic workforce solutions for qualified companies investing in Georgia.
Quick Start helps companies assess, select, and train new hires. Services are provided free of charge as a discretionary incentive for job creation for clients opening or expanding manufacturing operations, distribution centers, headquarters operations, and customer contact centers in a broad range of industries.
GPA grew its workforce by 145 employees in 2021. Lynch says the increase is due in part to Y.E.S., a workforce development program aimed at career-ready high school seniors, launched by GPA in early 2019.
The program, which has accepted 26 students to date, has been so successful that GPA recently expanded the Youth Learning Equipment and Safety/Youth Elevating their Skills and Training program, now known as Y.E.S.+
The initiative previously focused on terminal operations and maintenance positions, but Y.E.S.+ will begin including other departments such as finance and human resources when the 2022 program kicks off in August.
Partners in Growth
Connectivity and communication go hand-in-hand in the supply chain, and the state’s emphasis on forging strong links all along the way is a vital factor in Georgia’s logistics success. Nowhere is this aspect of Georgia’s logistics leadership more evident than the links that exist with its ports.
“The people we deal with at the Georgia Ports Authority are always on their game,” says Hal Justice, vice president of sales and operations for Atlanta Bonded Warehouse (ABW), a long-time provider of temperature-controlled and ambient warehousing, co-packaging, and LTL/TL transportation services.
National and international logjams made the past two years particularly challenging for logistics providers, Justice acknowledges. But, he says, timely, open, and reliable communication helped minimize the stress of short inventory and limited flexibility in outbound transportation.
“Our contacts at the port are very upfront, very responsive,” Justice says. “They give us the facts-on-the-ground so we can communicate expectations accurately to our customers.”
The experience is typical of the cooperation that exists among the key links in Georgia’s supply chain. “We rely a lot on drayage from the port,” he says. “The drayage carriers and railroads were responsive. Everybody was working to fix the problems. Everybody put a shoulder into it.”
This positive logistics environment contributed to another year of growth for ABW, which annually handles more than 700 million cases and 9.4 million pallets across 6.4 million square feet of space from 15 facilities across the Southeast and Southwest.
“We added a lot of business in the back half of the year,” Justice says, “and our throughput volumes were up more than 14% over 2020. This increase was in spite of short inventories.”
The continued record of growth is especially remarkable in light of the unpredictable nature of 2021’s inventory needs, stretched transportation resources, and evolving health regulations brought about by the pandemic.
“To say that 2021 was a challenge would be an understatement,” Justice says. “Some customers had no issues with getting us inventory but those were the exception, not the rule.”
Rising to the Challenge
Employment challenges likewise complicated matters, but Georgia employers such as ABW rose to meet those challenges.
“We have never seen a year quite like last year for scheduling labor on top of finding, recruiting, and retaining a skilled workforce,” Justice says, adding that ABW emphasized—and continues to emphasize—the importance of maintaining a skilled workforce whose primary focus is serving the customer.
Among other things, competitive wages figured prominently in the solution. “If you don’t have enough applications to cover your growth and turnover, you are not offering a competitive starting and mature wage,” he says.
Finding solutions, in turn, contributed mightily to Georgia’s ability to maintain its status as a standout on the national logistics landscape by distinguishing the state from other regions of the country. “We had several large customers shift out-of-region volume to us in spite of a transportation penalty simply because we could handle their orders,” Justice says. “It was difficult, but we have a great operations team who figured out a way to handle the volume.”
Plentiful Resources
As its name suggests, nVision Global Technology Solutions takes a world view of logistics. From its perspective, Georgia is more than just a peach—it is a veritable orchard of logistics resources. And to keep the crops growing, water is as essential as the sun.
“Georgia continues to thrive in the supply chain,” says Stewart Dunsmore, senior vice president, supply chain services, at nVision Global. “This is driven by many activities such as the Savannah Port providing more access for larger vessels and additional open space for volume.
“Also, many shippers have made Georgia home for both corporate offices and logistics operations along with the distribution facilities required to support their growth in the Southeast and up and down the Eastern Seaboard,” Dunsmore says.
Georgia seaports have long been considered to be among the top ports in the United States, serving as gateways to the world. But, Dunsmore says, there’s more to the state’s “liquid assets” than just that: “Georgia has inland ports as well,” he points out. “Atlanta is one of the largest ports for both rail and air activity. Additionally, Georgia has a very extensive Foreign Trade Zone network throughout the state.”
As a world leader in end-to-end order management, nVision Global also enjoys a unique perspective on the progress achieved through supply chain digitalization.
“We have spent more than 30 years designing and developing some of the best solutions worldwide to address global freight management,” Dunsmore says. “Today, in the world of ‘digital order management,’ the old manual processes that were previously involved with global logistics have been replaced with a faster and more efficient digital approach.
“Our solutions provide customers with a frictionless experience to quickly deploy and evolve configurable technology solutions around their constantly changing requirements,” he adds.
All of this translates into enabling nVision’s customers to leverage the company’s cloud-based order-management platform, real-time intelligence tools, and customizable reporting to manage their day-to-day supply and demand chain activity.
“Our customers rely on this technology across every aspect of their business to ensure they deliver for their customers,” Dunsmore says. “Our global spend management solutions are built upon the cornerstone of our technology services—our pricing, rating, and auditing technology. These tools drive our worldwide robust freight auditing services.”
The company’s proprietary freight audit and payment technology is the most advanced in the market, according to Keith Snavely, nVision’s senior vice president, global sales and marketing. “Our solutions are built on Microsoft DNA, our web portals are user-friendly and focus on real-time visibility and transparency,” he says, adding that new system updates are released monthly.
The financial return for freight audit goes well beyond the errors identified during the audit process. “As it relates to freight audit and spend management, the potential savings are hidden in the details,” Snavely says. “Something might seem simple at a first look, but upon further analysis with comprehensive spend management solutions, our customers maximize their returns. Freight audit and payment is just the first step in global transportation spend management.”
Snavely says nVision’s extensive experience in transportation and logistics provides the company with a comprehensive understanding of all the peculiarities of freight invoice data.
“It helps us to understand how to harmonize charge items as well as global origin and destination data,” he says. “Our analytical tools are optimized to deliver detailed insights on specific line-item charges, freight, shipments, and much more.”
Thinking Ahead
The rapid changes and ever-increasing demands in today’s logistics marketplace require logistics providers to keep pace with—and anticipate—growth as never before. Fortunately, forward thinking is yet another way in which the state’s logistics providers have contributed to the state’s leadership in the industry.
Case in point: JIT Warehousing & Logistics, a Georgia family business with more than three decades of experience in the import/export field.
Located just a half mile from the GPA’s Ocean Terminal and about 3.5 miles from the Garden City Terminal, JIT—which stands for Just In Time—provides warehousing, trucking, shipside delivery, port pickup, container drayage, stripping, stuffing, cross-docking, and over dimensional/crane services. The company’s over-dimensional division includes local road escort, rigging, cargo transfer on and off flat racks, securement to line requirements, and additional specialized trailers for heavy haul.
In response to increasing demand, JIT is now expanding both its vehicle fleet and its facilities. “We are expanding our over dimensional department,” reports Ben Goldberg, company president. “We’ve added a new heavy-haul truck and three heavy-haul trailers. We’ve also opened a second yard to service import and export over dimensional loads.”
Goldberg says JIT is putting a crane at its second Savannah heavy lift facility, enabling the project cargo division to handle heavier lifts at both yards.
Trevor Lockwood, JIT’s vice president, project cargo, says the new equipment will enable JIT to significantly increase its capacity to assist importers and exporters with their project cargo needs.
Additionally, the company is breaking ground on a new 226,000-square-foot rail facility to service cargo to and from Norfolk Southern. JIT operates facilities on the Norfolk Southern rail line, in addition to several other Savannah locations, offering more than 750,000 square feet of warehouse space.
The fleet and warehousing footprint expansions coincide with the GPA’s port expansions. “We’re excited about bringing online our new warehouse with Norfolk Southern rail line,” says Evelyn Goldberg-Davis, JIT’s executive vice president. The company is working with Norfolk Southern to transload more boxcars to ocean containers and ocean containers to boxcars.
“With additional trucks and company-owned chassis, our container volumes continue to increase,” notes Anna Lockwood, vice president.
The company’s driver dispatch software links with the port authority system for continual container updates. “Due to our variety and capabilities, we are a first call for problem solving for many of the lines and entities that work alongside the GPA,” she says.
For company founder and patriarch Ben Goldberg, it all adds up to maintaining the company’s place as a star on Georgia’s logistics crown. “I’m very proud of our family’s roots in Georgia,” he says. “And you can be sure we will continue to study our assets to stay ahead of the curve.”
Anticipating Needs
The exchange of data between various heterogeneous systems is a major challenge for logistics, says Steve Syfan, executive vice president of Syfan Logistics. Located some 50 miles northeast of Atlanta in Gainesville, Syfan is a full-scale, asset-based logistics management company and a well-recognized logistics leader in Georgia.
“We have been developing a digital footprint that places us in a strategic position to rapidly handle these challenges,” Steve Syfan says. “Leveraging relationships with technology partners inside and outside the logistics space allows Syfan to think outside the box and provide creative solutions to industry issues.”
Syfan believes Georgia’s technology infrastructure is one of the most redundant and robust of any state. The Atlanta region, he points out, is the hub for several large carriers and service providers.
“The state has always placed an importance on economic development, which attracts businesses to the state and creates an environment for existing businesses to grow,” Syfan says, adding that Syfan Logistics distinguishes itself as a particular Georgia logistics asset in part through the broad reach of its offerings.
Cultivating Solutions
“Syfan is diversified with a network of services to provide much more flexibility in addressing virtually any need of a shipping customer—from third-party brokerage representing thousands of carrier partners to its own fleet of trucks for dedicated loads or filling in gaps,” he says.
“Syfan also has a sister company that provides terminal tractors and trailers for fleet leasing or new sales to warehousing and distribution customers,” Syfan adds.
He says Syfan Logistics embraces technology “not as the driving force of logistics, but as a tool to extend the services offered to partners, and act as an advocate for the industry’s digital transformation.”
Like allbusinesses, logistics has been impacted by nationwide employmentchallenges. One way Syfan copes with the challenge of finding sufficient qualifiedworkers is to tap into the state’s rich logistics education assets.
“To meet our region’s need for a professional logistics workforce, our company is proud to partner with the University of North Georgia in nearby Dahlonega to create the area’s first supply chain academic curriculum and logistics laboratory,” Syfan says. “We are always looking for innovative ways to build a larger pool of quality professional candidates for our industry and our growing company. We believe this collaboration with UNG will expose many more students to career opportunities in logistics, helping them while building an even stronger workforce in our backyard of Northeast Georgia.”
Syfan has an extensive internship program that exposes potential team members to the industry. Company CEO Jim Syfan, who worked with the University of North Georgia on this project, was recently appointed by Gov. Kemp to the University Systems of Georgia Board of Regents.
Meanwhile, Steve Syfan, who serves on the board of directors for the GDEcD, looks forward to the planned 104-acre Northeast Georgia Inland Port, set for completion in 2024. The inland port will provide a direct link to the Port of Savannah via Norfolk Southern.
Providing Proven Expertise
Georgia’s infrastructure advantages certainly are key elements of the state’s logistics success. “Atlanta Hartsfield-Jackson International Airport and the Port of Savannah remain tremendous assets for Georgia logistics,” says Brian Thompson, chief commercial officer for SMC³.
But expertise and innovation are equally vital. As a leading provider of logistics intelligence solutions, SMC³ plays a critical role in facilitating high-speed, electronic communication between carriers, shippers, and third-party logistics providers across North America. With corporate headquarters in the Atlanta suburb of Peachtree City, SMC³ enjoys a solid track record of pushing the LTL industry forward for more than 85 years.
“Georgia is a top state for doing business,” says Thompson. “It has nationally ranked infrastructure and IT operations to effectively reach domestic and global markets, so Georgia plays a huge role in effective supply chain operations.”
SMC³ offers a range of freight transportation solutions that contribute to Georgia’s logistics prominence. Thompson says the company is uniquely positioned to help customers of any size across the continent, including those with diverse requirements.
“Our products continue to support customers’ needs as they grow, whether they’re a shipper dealing with 10 shipments per week or a logistics service provider handling 10,000 shipments per day—or a carrier transporting those shipments,” Thompson says.
Focused on Solutions
SMC³ delivers solutions for those requiring high-powered tools to support transportation optimization and advanced modeling as well as those seeking simpler, secure solutions, he adds.
For example, Thompson says, shippers look to the company’s over-the-road transportation procurement solution, Bid$ense, to optimize freight spend and streamline transportation planning. LTL carriers share data and shipment information via APIs (application programming interfaces) and EDI (electronic data interchange), and SMC³ offers solutions for both methods of communication.
The company continues to develop new technology solutions all with an eye to what Thompson calls a simple truth: “The introduction of innovative supply chain solutions into established supply chain processes is the best way to solve complex transportation issues,” he says. “This has never been more evident than during the pandemic.”
SMC³ offers CarrierConnect XL, a solution enabling LTL carriers to communicate operational capabilities, such as lanes served, published transit times, and direct/indirect points. In 2022, the company is enhancing the program with advanced messaging capability that allows carriers to communicate location and lane-specific service disruptions directly into the shipper’s transportation management solution (TMS).
“The carrier can inform their customers about when the disruption begins, ends, and the reason for the disruption such as a storm, hurricane, fire, or even capacity constraints,” Thompson says. “During a time of unprecedented supply chain challenges, it is imperative that information be available to all parties in a manner that is immediate, efficient, complete, and accurate.”
CarrierConnect augments the company’s existing suite of standardized API and EDI solutions that work to close the communication gap in LTL transportation.
Market Growth
In the end, the definition of logistics leadership is subjective and the factors that set one state or region apart are as numerous as customers’ logistics needs. This explains why Taylored Services is scheduled to open a new distribution site within 10 miles of the Port of Savannah in summer 2022. Taylored Services offers a range of high-quality and efficient logistics solutions that allow it to scale expeditiously to meet customers’ needs.
“Over the past few years, we tracked all the key renovations that the Savannah port has achieved to accommodate larger ocean vessels,” says Mike Letzter, Taylored’s vice president of distribution and fulfillment. “Taylored Services feels this is the next strategic port for our company growth to support our customers.”
The company, celebrating its 30th anniversary this year, is building on its established record of success in New Jersey and California, near the ports of Elizabeth (New Jersey) and Los Angeles.
“Taylored Services has been recognized as a Top 100 logistics company for the past seven years due to our company growth, brand recognition, and omnichannel capabilities,” Letzter says. Savannah’s $1 billion investment in deepening the water level to accommodate the larger and wider ocean vessels has paid off, he adds, making the port the third largest in the United States.
“Savannah’s commercial real estate has been booming with new distribution sites over the past few years, so Taylored wants to participate in this regional market growth,” Letzter says. He notes that Taylored’s employee-centric culture meshes well with Georgia’s existing workspace. “We feel our company culture will be a terrific fit with the existing Georgia workforce,” Letzter adds.
“Taylored Services has doubled our revenue growth from 2015-2020, and then doubled again over the past year, which has created tremendous job growth for our current distribution markets,” Letzter says. “We see Georgia as another strategic region to establish these employment opportunities that are beneficial for us and the local job markets.”
The company has adjusted to the labor shortfalls that have occurred since the pandemic. “Our job market has been affected through economics, fear, illness, and government intervention regarding compensation, which encouraged the labor force to consider staying home instead of continuing employment,” he says.
“Taylored Services had to pivot off of our normal labor strategies to overcome these challenges through enhancing our work environments to be even more employee friendly to encourage the workforce to return and be retained,” Letzter says. The company enhanced its workplace environment through weekly prize raffles, onsite food trucks, performance bonuses, and competitive wage adjustments.
The company plans to be a major contributor to Georgia’s logistics culture in ways that go beyond the workplace. “Historically, Taylored Services has been a strong supporter and contributor to local communities and school environments through volunteer work and financial support,” Letzter says. Taylored also takes pride in being a “green” company, with company policies and procedures designed to ensure a high level of recycling.
“Taylored Services has been built on flexibility, innovation, and fearlessness over the first 30 years,” Letzter says. “We will continue to pursue these same core values as we move forward into Georgia.”