Providing Inbound Freight Visibility and Enhancing Savings
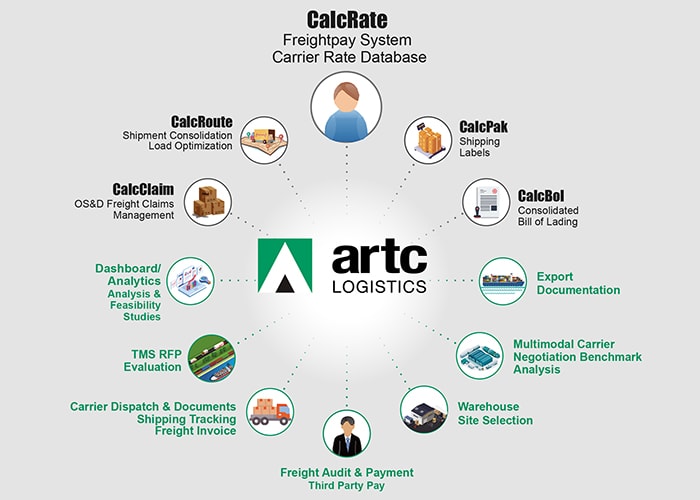
When a client grappled with vendors that incurred excess freight charges, ARTC Logistics implemented a system that brought visibility and streamlined the inbound shipment process.
The Challenge
When it comes to carrier selection for freight, shippers have control of their outbound shipments, using parameters like cost, transit time, dependability, and history of claims to make the optimal choice.
Inbound freight is a different story with vendors selecting the carriers, often based on their own preferences, which may or may not align with those of the consignee. Our client has been generating inbound routing guides for their vendors based on shipment weight, origin, and our client’s inbound warehouse.
Most vendors showed good compliance with the routing guides, but three vendors were notoriously poor with their routing, rarely matching the guide when shipping and generating excess freight charges of $40-50 thousand quarterly.
The Solution
Working with our client, we instituted ARTC’s Vendor Portal for inbound routing. Our client synchronizes their order file with the portal. When vendors are ready to fulfill orders, either partially or fully, they log into the customer’s branded web page. The portal lists all of the open orders for that vendor. The vendor selects any orders that are ready to ship and enters the number of items if the order is incomplete.
The system then provides the preferred carrier and terminal information and can even tender the load automatically. If the vendor does not use the system-selected carrier, a reason is required. The vendor can then be charged back the difference in freight costs if there is not a valid reason for rerouting the shipment.
Initially, compliance was poor but after a few chargebacks, compliance increased to the point where they were no longer necessary. Our client ended up saving almost $200,000 in the first year.
The system assigns a PRO number and stores the shipment information in the accrual file associated with CalcRate, ARTC’s TMS. Shipment notification is transmitted to the customer in advance, which helps with planned receipts and is also used to track and trace the shipments, giving our client visibility to their inbound freight for the first time.
The improved level of detail was helpful in renegotiating inbound freight charges, further enhancing their savings. In addition, the inbound shipment costs were accrued in the freight payment system—streamlining the subsequent freight invoice reconciliation/audit process.
To learn more:
[email protected]
212-736-8565 Ext. 3045
www.artc-logistics.com