Conveyor Upgrade Increases Warehouse Efficiencies and Order Volume Capacity
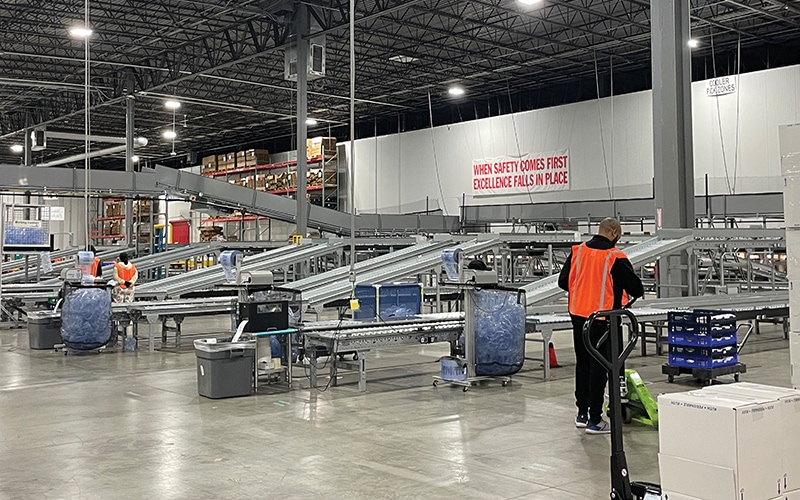
MD Logistics implemented a tailored conveyor solution in its warehouse to serve clients in the life sciences and pharmaceuticals industry. The new configuration boosts flexibility, efficiency, and output.
The Challenge
Over the past few years, the life sciences and pharmaceutical industries have witnessed tremendous growth. Advances in temperature-sensitive biologics and global events have increased the need for readily available storage environments and require an efficient way to process the added volume of orders.
As our clients have increased their own product volumes, the challenge for us as their 3PL partner becomes: What improvements can we make to our processes to more efficiently move product throughout our facility?
The Solution
In a state-of-the-art life sciences and pharmaceutical warehouse, conveyors are an efficient way to move product throughout the facility. In the MD Logistics warehouse, we have found success with utilizing conveyor automation in our pick-pack area, by moving shippers to be picked with product, then audited and packed out before being moved and staged for shipment.
As order volumes begin to increase in our warehouse, it very quickly became apparent we had reached the maximum potential with our existing conveyor configuration. With current clients anticipating future organic growth in the coming years, the decision to replace the existing, tired conveyor with new, efficient automation was clear.
Working with an external vendor, we were able to procure and implement new conveyor automation in one of our state-of-the-art warehouses, servicing clients in the life sciences and pharmaceuticals industry. This new configuration has proven to provide a variety of benefits for our warehouse team:
Flexibility. Working with a vendor who specializes in warehouse conveyors, allowed us to fabricate a tailored solution not only to our existing floor plan, but also to the specific needs of our clients. We were able to build a system tailored to our warehouse floorplan, taking the time to plan out current volumes while anticipating future volumes to allow the system to evolve as the needs of our clients do as well.
Efficiency. Perhaps the largest pain points with our original conveyor system were the inefficiencies that were apparent as our client’s business grew and order volumes increased. As our workload increased, our warehouse teams were compensating with increased physical labor—lifting shippers onto the conveyor, walking old corrugate to the compactor, and moving shippers from the conveyor to the staging area to be loaded on outbound trucks.
All of this extra movement from our team added extra time to the process and created inefficiencies felt across the operation. The new conveyor system has allowed us to be more intentional with the space that we have, while reducing the extra effort and physical labor that was previously placed on our team members.
Overall, this has led to a more efficient process where we have already been able to reduce team member “touches” by 50%.
Increased Output. Being able to tailor a system to current and future needs provides us increased efficiencies to be able to handle additional output. These changes have allowed our team to increase our order fulfillment capacity by 25%, with the potential to handle additional volume as our client’s business needs evolve.
To learn more:
[email protected]
317-838-8900
www.mdlogistics.com