The Model Port of the Future
Tags: Global Logistics, Logistics, Ports, Supply Chain
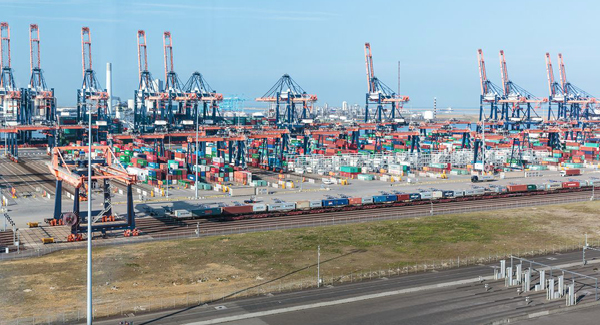
The Port of Rotterdam, Europe’s largest port, is working with IBM on a long-term digitization strategy that will transform the port—not only to improve safety and efficiency today, but also to accommodate autonomous ships, as well as process and ship metal 3D-printed ship components on demand in the future.
Key elements of the digitization strategy include:
- IoT-enabled sensors and AI capabilities will measure and analyze weather, water, and communications data from IBM’s The Weather Company. Data insights will be used to reduce wait times, allow more ships to enter the port, and predict the best time, based on water level, for a ship to arrive and depart Rotterdam with the maximum volume of cargo loaded on board.
- IBM IoT technologies will power a single dashboard that displays real-time data from multiple parties—terminal operator, ship’s captain, the port—enabling safer and more efficient traffic management at the port.
- Shipping companies and the port stand to save up to one hour in berthing time, which can amount to about $80,000 per hour in savings. When multiplied across the 140,000 ships entering the port every year, this means that the port will be able to dock more ships while shipping companies reduce costs each time they dock at the Port of Rotterdam.
- Digital dolphins, smart quay walls, and sensor-equipped buoys will provide insights on the condition and utilization of a berthing terminal and the surrounding water and weather conditions, enabling port operators to identify the optimal time for ships to dock, and where and when they can do so.
- As part of a multi-partner initiative, IBM cognitive IoT technology is being infused into a production process that uses a robotic welding arm to apply high-quality metal layer by layer to create ship components such as propellers, on-demand and faster than ever before—from six to eight weeks to just 200 hours.