AMRs Move Dock-to-Stock Metrics in the Right Direction
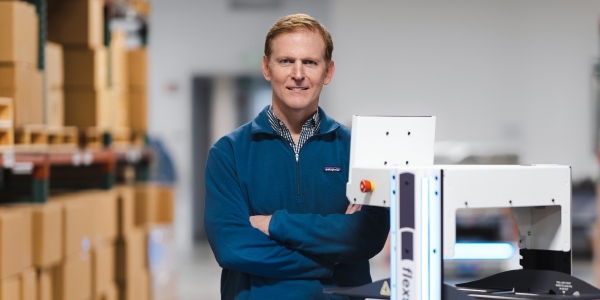
Manufacturers, 3PLs, distributors, and retailers are under pressure to get goods picked, packed, and shipped faster than ever. Here’s the thing, though: it will be difficult to get orders out the door on time if raw materials or pass-through inventory aren’t processed efficiently.
That’s why any conversation about improving outbound processes—especially when exploring automation as a solution to fulfillment problems—has to look at increasing inbound logistics efficiencies. Fortunately, many decision-makers are starting to understand this.
The Push-Pull Effect
Warehouse and distribution center (DC) operators want to quickly get autonomous mobile robots (AMRs) online in their facilities to speed fulfillment and improve inventory throughput. Insufficient workers are available to meet demand, especially during peak periods, so operators need a flexible automation solution to augment the workforce.
Interestingly, it isn’t always the final pick, pack, and ship processes that are bottlenecked by climbing order volumes, shrinking lead times, and labor stagnation. This issue is becoming even more apparent as AMRs are rolled out in outbound workflows. Workers are most certainly walking less, which gives them time to pick and pack more orders and the ability to report significant efficiency and throughput gains. Despite this improvement however, fulfillment challenges remain.
This drives decision-makers to audit operations more holistically, revealing that receiving and replenishment workflows—which have yet to be similarly automated—are a root cause of inefficiency and quality errors. Workers struggle to get inbound materials and products put away or cross-docked because processes remain manual and laborious, even when forklifts and other machines are used.
The volume of inventory unloaded every day multiplies at record rates as customer demand balloons. So, even though workloads for inbound and outbound teams are equally affected by order surges, outbound teams perform better due to AMR support.
As a result, warehouse and DC operators realize that pushing teams to get more products out the door must be balanced with pulling more AMRs into inbound environments. This equilibrium is key to improving the dock-to-stock cycle times needed to keep up with high-velocity outbound operations.
Warehouse and DC operators see growing value in autonomously transporting material and goods to the correct bin locations so there’s a steady flow of inbound inventory to order fulfillment locations.
Boosting Performance
Flexible automation is a fairly new concept, especially to those who have used fixed automation for decades. On-demand automation solutions, such as cloud-based AMRs or robot-as-a-service (RaaS) offerings, are very different from the long-term, capex-intensive commitments required of most other automation platforms.
At its simplest, when dock-to-stock cycle time is optimized with AMRs, then follow-on picking, packing, and shipping workflows can be boosted to higher performance levels.
When the entire operation moves like a well-oiled machine, the result is happy and satisfied employees, shareholders, partners and customers.