5 Phases of Disruption Response
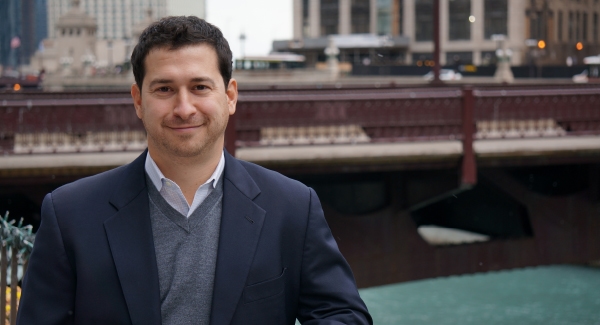
While supply chain problems appeared at first to be temporary ramifications of the pandemic, research now suggests that restoring previous supply chain functioning will take more than time. New solutions will have to be developed, and innovation in the tech space will have to be part of these solutions.
In a recent presentation, Palash Barandwaj, vice president, industries, for SpringML, an artificial intelligence (AI) solutions provider, identified five phases of supply chain disruption response and described use cases for cloud-hosted AI and machine learning (ML) technology in each.
These are the main takeaways from each section of the presentation.
1. Adjusting Operations on the Factory Floor. Supply centers can implement measures to improve supply-side efficiency as soon as a crisis occurs.
When the supply chain is disrupted, a bottleneck develops on the factory floor. AI and ML technology can’t actually remove the backup of supply from the warehouse, but it can make managing the backup more efficient. Smart sensors on the factory floor can monitor fluctuating supply and demand and manage production while each fluctuates.
Virtual reality, augmented reality, and manufacturing release can also be used to simulate production scenarios, bring in reinforced learning, and optimize specific processes. This solution also produces opportunities on the business side.
2. Reacting to Disruption. When it first occurs, disruption might look like a problem that needs to be solved immediately with bodies on the ground, but operational awareness is just as crucial in these scenarios. AI helps businesses bring visibility to shipment issues, as well as facilitate digital transformation and enable Internet of Things analytics to support what Barandwaj calls “the whole operation side.”
In a complex supply chain, warehouse managers want to trace all the bottlenecks and collect data on inventories and returns. A robust analytics framework can do as much to combat disruption as any operational mechanism put into practice.
3. Responding to Consumer Demand. This requires looking at the overall supply chain ecosystem to identify gaps and shortages. With this data in place, AI can be implemented to develop a digital shelf.
Using the digital shelf, suppliers can accurately estimate shelf capacity and track metrics like decline in capacity, availability of certain products, and freshness of different foods. AI sensors and Vision AI make it possible to monitor every aspect of inventory levels.
4. Addressing the Labor Shortage. Suppliers should develop a more dynamic plan than setting up a help hotline and hiring a staffing company. Using AI, suppliers can develop a portal that identifies potential hires based on specific labor needs. They can target hiring based on labor shortages and needs in specific areas, not just overall numbers.
5. Preparing for the Next Crisis. The current supply chain crisis is advanced, and will take time to fully resolve. This is all the more reason to better prepare now for the next crisis and do all that we can to reduce that time and lift as much as possible.
For Barandwaj, this means using AI to develop a “digital train” that can simulate real factory processes so warehouse managers can look at the data these processes generate and respond accordingly. Planning for a disruption, such as a water shortage, ahead of time using a digital train allows decision-makers to predict drought levels and assess the attendant level of risk.
Using reinforcement learning, supply-side professionals can prepare ahead to take the appropriate actions when problems of this kind occur again.