Ins and Outs of DC Efficiency
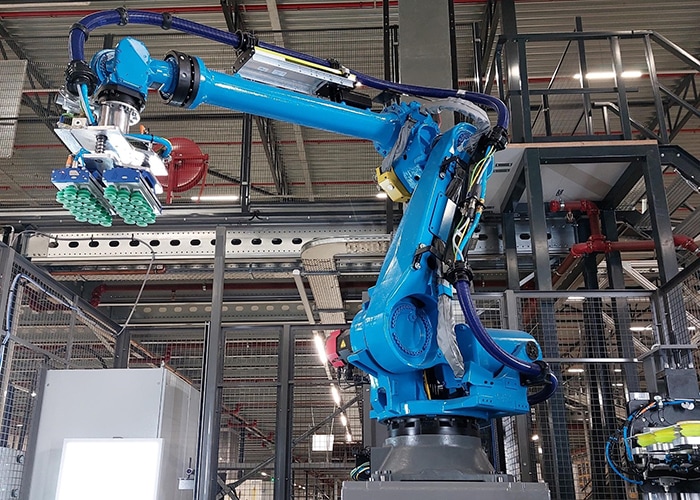
Growing SKUs, a labor shortage, and demanding customer expectations are driving many companies to enhance and automate their distribution center operations. Take a look at what they are doing.
“A virtual warehouse on the ocean.” That’s how Shannon Freise, senior vice president, operations, with Sager Electronics, a North American distributor of power products, describes the solutions and processes she and her team use to monitor products coming from multiple overseas carriers.
Until a few years ago, Freise and her colleagues lacked solid visibility into the products headed to their North American distribution centers from abroad. That changed when they implemented a solution that consolidates shipment information to offer visibility into arriving shipments.
Now, as soon as a bill of lading shows a product has shipped from a supplier, Sager Electronics receives notice and logs the inventory into its virtual warehouse.
At the same time, the sales staff can let customers know approximately when their orders can be filled. When products arrive at the physical warehouse, they’re moved through an efficient bin-to-bin transfer. Accounting is streamlined, because Sager has already identified the inventory it owns.
Like Sager, many companies are enhancing and automating their distribution center (DC) operations.
“Pressure for distribution and fulfillment (D&F) operations to perform has never been greater,” says Keith Fisher, president of Honeywell Intelligrated, a warehouse automation solutions provider. Multiple factors—exponential growth in stockkeeping units, the labor shortage, and rising customer expectations—are driving factors.
Inbound Processes
“The optimization of inbound operations is an area that is easily overlooked,” says Billy Carter, vice president with Tompkins Solutions, a supply chain services firm. Yet more efficient processes here can rein in fulfillment and other costs.
For example, a robust vendor compliance program can streamline inbound processes. Suppliers who’ve earned high grades for historical performance and reliability generally require less auditing and their pallets can quickly be received and put away from the dock.
Several other common-sense tactics can boost receiving efficiency. For fast-moving products, BroadRange Logistics, a global consolidation services provider, allocates dedicated space close to the dock doors and away from any heavy products.
It also implements efficient receiving processes, such as cross-docking for products that need minimal handling. The BroadRange team regularly updates customers on their inventory levels, reducing the risk of overstocks, stockouts, and obsolescence, says Amit Agrawal, marketing manager.
An inbound put-away audit is another best practice. After product is received and moved into storage, a separate audit is performed to ensure the product was placed in the correct location and with the valid quantity.
“Operations that perform put-away audits see better cycle count results,” says Gary Meador, chief operating officer with third-party logistics provider ODW Logistics. “They also have fewer issues with inventory that can’t be found.”
Inventory levels
Given recent delays in products coming from overseas, more organizations are boosting inventory levels. With warehouse space generally tighter than it has been in the past, however, DCs need a solid handle on the goods they’re receiving.
They should scan at least one of each case to understand quantity and size, suggests Greg Meyne, senior director of automation with enVista, a provider of supply chain technology and services.
For instance, storage and picking needs will differ for a shipment of 1,000 units that consists of 100 cases of 10 units each, versus a shipment of 200 cases of five units each.
“We can’t overstate the importance of data,” says Rob Thyen, senior vice president-solutions engineering with GXO Logistics.
By leveraging data, artificial intelligence (AI), and analytics tools, it’s possible to collect and analyze data on nearly every aspect of warehouse operations.
“By using data to identify patterns, trends, and areas for improvement, we can make more informed decisions,” Thyen says. For instance, it likely makes sense to move fast-moving items where they can be more easily accessed.
Robot Costs Come Down
Deploying robots within a DC has become increasingly economical.
“Better camera technology, keyword image recognition, more computing power, and ever-improving AI are increasingly opening fields of application in intralogistics,” says Karoline Kowalik, logistics engineer and PhD researcher with Arvato Supply Chain Solutions.
By using an AI camera that snaps images of different parcels, robots can learn to handle thousands of SKUs of varying sizes. How? Once the robots learn how to handle one parcel of a particular size, they can try to handle similar packages the same way. If they don’t receive an error message, the robots can assume their actions were correct.
When designing Sager’s new warehouse in Lewisville, Texas, Freise knew it didn’t make sense to install miles of conveyance, as the products’ weight made them too heavy to use conveyors. Instead, Sager will deploy robots to transport products.
As products arrive at the Texas distribution center, robots will transport carts from the receiving dock to vertical lift modules (VLMs) for stocking, and then from the VLMs to packing.
“For products that are too large for traditional conveyance, we’re moving the product less,” Freise says. “Instead, we invested in solutions to make it easier for the individual to move to the product.”
Accuracy and streamlined operations are just as critical within outbound processes. Agrawal identifies several strategies his firm employs to achieve this, including batch picking to group similar orders and reduce search and pick time. Pickers are assigned to specific zones within the warehouse to minimize travel times.
Arvato uses a robot-controlled de-palletizer, Stark, along with the warehouse management system, and an automated guided vehicle (AGV) to move cartons of different sizes and shapes from stored pallets. When the AGV brings the pallets, Stark picks the right amount according to the WMS.
At the picking positions, AI cameras measure the parcel and pallet dimensions, and calculate an optimal picking sequence and gripping positions. The cameras also detect different labels and orient the box accordingly.
Stark’s self-learning software can determine the shape of the object and how it needs to be picked up. Its flexible gripper head moves over the pallet, and suction cups lift the carton onto the conveyor belt.
Goods-to-person (GTP) systems regularly prove to be more efficient than traditional module/pick tower designs, as they reduce walking or travel time, Carter says. A well-designed GTP station can also be used in conjunction with many types of automated technologies such as autonomous mobile robots (AMRs) and shuttle systems.
Redesigning the sortation function can also yield efficiencies. In a traditional workflow, shipments are picked up by a carrier and typically sorted several times: at a local facility, a regional hub, and a destination facility.
In contrast, advanced sortation systems allow packages to be pre-sorted at the fulfillment center, which can leverage a “zone skipping” sortation strategy that eliminates stops between the fulfillment center and delivery.
Another area many DCs are re-examining is packaging. Properly sized boxes can cut transportation costs—no more paying to ship air—and shipping’s environmental impact. Some solutions can design cartons to fit the product being shipped.
“Building a box to fit is becoming a very big deal, because the payback is so prevalent,” Meyne says.
Planning and Communication
While technology is critical to effective DC operations, internal processes also need to be solid. A starting point is an efficient critical path, or the sequence of activities that must be completed between the start and conclusion of a process or project. Together, these activities make up the shortest possible duration of the project.
“If your critical path isn’t robust and operating efficiently, neither will your D&F operations,” Fisher says.
As shippers and logistics providers examine their operations, Fisher says they’ll want to ask multiple questions, including these: What steps can be automated? Is my software, or lack of it, hampering processes? How much automation makes sense for my facility?
Open, ongoing communication is critical. Take the case of expedited deliveries. Nicole Glenn, founder and CEO of Candor Expedite, which specializes in mission-critical and time-sensitive deliveries, says the need to expedite often occurs because of a break in communication. For instance, miscommunication between purchasing and production may cause a plant to start production, only to realize it’s missing a key component, which then needs to be expedited.
One step that can help to avoid misunderstandings is to minimize second-hand communication. For instance, the IT reps in the warehouse should speak with the vendor’s or customer’s IT reps, rather than have the salesperson mediate, says Khadar Mohammed, business solutions architect with Tecsys, a provider of supply chain management software.
A robust planning process and visibility are also essential, Mohammed says. Visibility to incoming work makes it possible to put in place the people and resources needed to execute the plan.
Standardizing processes minimizes wasted time by ensuring operational consistency and accuracy. This includes establishing procedures for receiving, inventory management, picking and packing, and loading.
As DC operations become increasingly critical to performance, and with space and labor still tight, shippers and logistics companies need solutions that enable them to boost accuracy and streamline processes.
“The old days of adding more buildings and people, and muscling your way through have come and gone,” says Jeff Wolpov, senior vice president of ecommerce for Ryder E-commerce by Whiplash. “You need to focus on efficiency and productivity, and invest in systems and processes.”
A Vertical View
Here’s how leaders in several verticals are tackling distribution challenges.
Retail. Ramesh Murthy is chief supply chain officer and executive vice president with Bob’s Discount Furniture, which operates 165 furniture stores across 24 states. Murthy and his team have been working to enhance operations at the company’s five distribution centers, which each support a different customer zone.
While each DC will continue to support a customer zone, Bob’s Discount Furniture is rolling out a multi-distribution center fulfillment solution. This will enable it to quickly make available to customers the products they ordered, regardless of whether they are in stock in the distribution center that’s actually closest to them.
So, if a customer makes a purchase in Connecticut, but the Connecticut DC is out of the product, the company can ship it from another, nearby distribution center. “The new solution will maximize customer service and build redundancy into our system,” Murthy says.
Murthy and his colleagues also are looking at artificial intelligence for exception recognition; this will help them gain a sense of where problems with incoming inventory might occur.
“The earlier I can figure out a problem, the faster I can get to a resolution,” he says.
Consumer Packaged Goods. Courtney Folk is co-founder and CEO of Renewal Logistics, which focuses on consumer packaged goods, among other verticals. Among the best practices she employs is requiring barcoding on all master cases and “eaches” so no items end up outside standard shipping and receiving protocols.
For instance, some cleaning solutions come in a case, with spray nozzles packed separately. To reduce the risk that the nozzles are forgotten when the solutions ship out, they also need to be scanned in and out of inventory.
Over time, procedures for addressing issues like this should become second nature, so employees spend less time asking managers how to handle them.
Fixing Mistakes
When a mistake is made, Folk and her team review the causes and put in place processes to keep it from re-occurring. This requires considering the cost of prevention, how often a problem is likely to reoccur, and whether it makes sense to, in some cases, handle one-off issues as they arise.
“In most cases, this is a great process for any company to use to streamline both inbound and outbound procedures,” she says.
Technology. Avnet, a global technology distributor and solutions provider, is expanding the business analytics capabilities of its logistics operations. “Our goal is to achieve breakthrough performance through predictive and prescriptive insights,” says Shaune Pittman, vice president, Americas logistics operations.
Gaining Visibility
One area of focus is gaining greater visibility into the volume and type of inbound deliveries received at Avnet’s warehouses. Currently, Avnet gets about 24 hours advance notice before shipments hit the receiving dock. Working with Avnet’s business analyst and business intelligence teams, Pittman aims to increase the forecasting window to 5 to 7 days.
With more advanced notice, Avnet will be able to boost efficiency in getting products from dock to stock and better manage resources, Pittman says.
He and his team also are working with carriers to get details on each purchase order as soon as they collect a shipment and load it into their system. Using business intelligence, they’ll combine the information into a single dashboard.
As of early April 2023, the analytics project was about 80% complete. When fully implemented, Avnet will be getting advance notification on, among other information, the number of parcels and pallets arriving each day, up to one week in advance. They’ll also have real-time access to order updates.
Pittman and his team will continue to refine the process, with a goal of reaching an accuracy level of 90%.
“Having this information available will allow us to schedule the optimal mix of resources needed at a given time and drive further efficiencies in our processes,” Pittman says.
Getting Out Quick
As their ecommerce operations grow, many shippers consider splitting inventory across multiple distribution centers so products are closer to more customers.
The hitch? If you only have, say, one dozen units per SKU, splitting them often isn’t practical, says Jeff Wolpov, senior vice president of ecommerce with Ryder Ecommerce by Whiplash. Instead, small parcel delivery is more economically friendly and accomplishes the same goal of moving goods to customers as quickly as possible.
When products arrive at a DC that will be used to fill ecommerce orders, it’s no longer enough to simply get them off the truck. “You need to separate and put them away so they’re sellable,” Wolpov says.
Sorting Out Parcel Picks
DHL Parcel and robot integrator AWL have developed a robot application that can pick and place parcels from a randomly mixed pallet onto the conveyor belt of a sorting installation.
The innovation combines robot-controlled AI-Vision with gripping technology, enabling packages of various sizes and weights to be placed on the sorting belt. The robot can lift up to 70 pounds and process 800 parcels per hour, automating work that humans previously did.
The diversity of parcels and the high speed at which the robot can depalletize is what makes this solution unique.
DHL customers deliver shipments on pallets, among other things. The pallet with, for example, various orders from a webshop, is placed in a pallet station. The robot places the parcels on the sorting belt to be sorted to their destination.
After the first application in its Rotterdam sorting center, DHL plans to implement the robot in other sorting centers.
Automated Materials Handling Solutions Amp Warehouse OpS
These automated material handling systems reach high places, pick and stack quickly, and provide flexibility to help your warehouse run smoothly.
BionicHIVE: The autonomous warehouse robotic fleet can climb racks from floor to ceiling. In an ongoing test through July 2023, Maersk is evaluating the BionicHIVE SqUID solution in its warehouse in Mira Loma, California (pictured). The solution can sort, pick, and replenish cartons directly to/from any spot in the warehouse racking. The mobile units are battery-operated, running a smart-power consumption module that automatically replaces its power packs. SqUID software integrates into warehouse management systems, providing real-time inventory data.
Interroll High-Performance Conveyor Platform (HPP): The new HPP from Interroll consists of standardized line and curve modules that can be combined to meet facility requirements, including straight conveyor modules and modules for inclines and declines. Able to process up to 10,000 units per hour, it can sort cardboard boxes, small packages, padded envelopes, manila envelopes, and polybags.
A42T Autonomous Case-handling Robot (ACR) from Hai Robotics: The goods-to-person solution extends upward, allowing facilities to store items up to 32 feet high, while remaining independent of any storage medium. The automated storage and retrieval system (ASRS) from Hai Robotics can handle most totes or container sizes and types—even cardboard boxes—on standard shelving structures. The A42T ACR provides the flexibility typically seen with AMR or AGV technology.
ACT from Logisnext Solutions: The ACT (automated compact truck) is the latest addition to Logisnext Solutions’ line of automated guided vehicles. The ACT can work with manual forklifts and handle the shelf processing of pallets and stacking in collaboration with the Mitsubishi PREMiA PBV20N3 Platform Pallet Truck. The ACT can also navigate narrow aisles and has a touchscreen and LED fins that show its current state from a distance for better communication with warehouse personnel. (Logisnext Solutions’ AGV operations are also known as Rocla AGV Solutions).
K55 Pallet Stacker AGV: The automated guided vehicle (AGV) from Kivnon can automatically transport palletized loads of up to 2,650 pounds and can lift them to a height of up to 59 inches. Equipped with lifting forks, the pallet stacker uses mapping navigation to perform cyclic or conditioned routes and can interact with other site vehicles, machines, and systems.
MasterMover AGV: Now incorporating BlueBotics’ ANT natural navigation technology as standard, MasterMover AGVs require no external infrastructure and use sensors to map their surroundings during training. Autonomous solutions are available from MasterMover with the capacity to move up to 66,140 pounds and can travel up to 8.2 feet per second.
BG Pouch System: The ecommerce fulfillment solution from BEUMER Group can streamline returns and save warehouse space. The BG Pouch System transports, sorts, sequences, and stores both outbound and returned items in a lean sequence, reducing the number of product touches in the returns process by more than 50%. Each module can handle more than 10,000 pouches per hour.
Kindred INDUCT: The high-speed robotic workcell is built on Kindred’s CORE/AutoGrasp artificial intelligence (AI) platform. It combines machine vision, grasping, and manipulation algorithms to automate the induction process for a variety of item sets, including boxes, envelopes, parcels, and packages. Powered by Kindred’s reinforcement learning-based AI algorithms, INDUCT workcells become more efficient over time.
RightPick 3 with the Suction Cup Swapper: RightHand Robotics introduced the Suction Cup Swapper (SCS) for its RightPick 3 system. The SCS gives the system the ability to switch the suction cup type on the fly in order to optimize the picking process for a wider range of products. RightPick 3 runs on RightPick AI software, which incorporates machine learning to improve picking over time. RightPick AI software enables the solution to handle thousands of SKUs from totes, bins, boxes, and cases.
ResGreen LilBuddy: The autonomous mobile robot (AMR) offers a compact size and natural feature guidance or magnetic tape hybrid guidance. It tows loads and drops them off automatically at a given location. With a 17-inch by 17-inch base, LilBuddy is one of the smallest AMRs in the industry. It can turn in place, making it ideal for narrow areas.