Supply Chains Are Social Networks
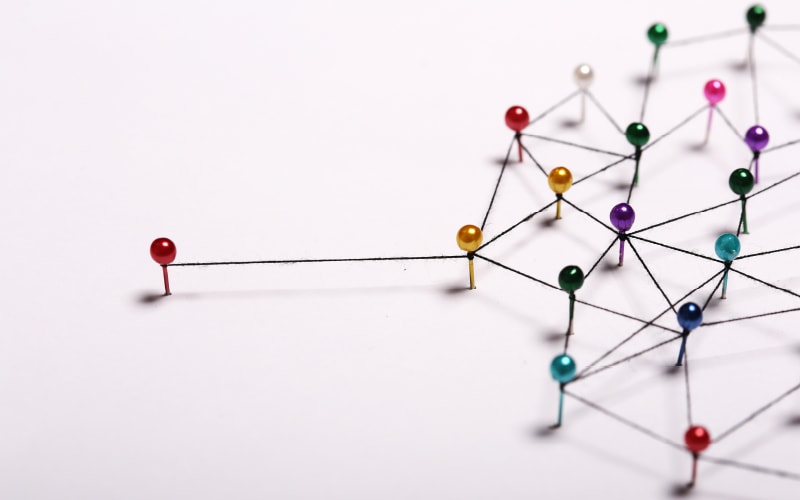
Technology dominates today’s economy. But, while many of today’s new business skills require technical knowhow, it is social skills, ironically, that may be key for future human employment.
Supply chains are more than just faceless corporations and transactional flows. The people in supply chain organizations have agency to direct and modulate those flows. When it comes to making decisions in a supply chain, such as managing exceptions or escalating problems, the personal relationships between the people in the companies and both their customers and suppliers matter.
As Lynn Torrel, chief procurement and supply chain officer at Flex, explained about the company’s operations during the pandemic, “We’ve had a few escalation calls with suppliers, and there are critical needs. Often, it’s someone I’ve known for many years. We had a hard negotiation and then had dinner and spent time together, and we always see each other at different events. That personal side is important, especially the relationships and trust that build over time.”
Person-to-person communications help provide unstructured information about what is happening and what each side is considering doing. It helps in negotiating a solution and obtaining mutual commitments to action.
“You can be as technically savvy as you want,” Torrel said, “but at the end of the day, you’ve got to pick up the phone and see if you can get a solution.”
Complex Relationships
Customer-supplier relationships in supply chains can be quite complex. Large organizations can have a web of personal relationships at supplier and customer organizations that span many levels or functions in each other’s enterprises.
Operational and administrative personnel might interact frequently to solve problems with purchase orders, shipments, and payments. Engineers in both organizations interact when working on new products and implementation of new technologies. Managers and executives hold strategic discussions and negotiations.
Companies often maintain teams dedicated to specific high-profile customers, creating long-term, person-to-person relationships. Good person-to-person relationships create a social bond that modulates how companies treat each other.

A mutually beneficial channel partnership between consumer product goods manufacturer Procter and Gamble and retailer Walmart creates inventory efficiencies through better coordinated supply chain activities.
To this end, Procter & Gamble, for example, has an office in Bentonville, Arkansas, next to Walmart’s offices. It is staffed with several hundred people, all dedicated to the P&G/Walmart relationship. There are so many vendors with similar offices around Walmart that the area has been dubbed “Vendorville.”
In the case of strategic customers and suppliers, the relationships can extend to the executive suite. For example, in dealing with shortages of pigments, Ignacio Pala, global sourcing director for colors at AkzoNobel, noted how relationships helped to address the shortage of a certain component.
“We eventually got it with the help of a dynamic cross-functional team, not to mention the support of our CEO, who kept the pressure on our suppliers to come through for us,” Pala said.
Similarly, when GM faced chip shortages after the 2011 Tōhoku earthquake, CEO Dan Akerson used his position on the board of chipmaker Freescale to seek an alternative source of chips.
“I picked up the phone, I called the CEO of Freescale, and I said, ‘I know you make chips of this type.’ We came up with a solution,” Akerson said.
An Industry-Wide Response
The social networks implicit in supply chains can extend beyond direct supplier-customer connections, as the case of a disruption at Evonik Industries shows.
On March 31, 2012, a tank filled with highly flammable butadiene exploded in one of Evonik Industries’ chemical factories in Marl, Germany. Intense flames and thick, black smoke billowed from the cyclododecatriene (CDT) plant at the 7,000-worker chemical complex in the heavily industrialized Ruhr River valley.
Roughly 130 firefighters fought the blaze for 15 hours to prevent its spread to the rest of the facility and to ultimately extinguish it. The explosion and fire killed two workers and severely damaged the plant.
Cyclododecatriene sounds like an obscure chemical, and the fact that it’s used to synthesize cyclododecane, dodecanoic acid, and laurolactam may mean nothing to most readers. But CDT is a key ingredient in making certain polyamides, which are high-strength plastics more commonly known as nylon.
In particular, CDT goes into a high-tech type of nylon—PA-12 or nylon-12—that is especially prized for its chemical resistance, abrasion resistance, and fatigue resistance. That makes PA-12 a favorite of the auto industry, which uses this tough plastic for fuel lines, brake lines, and plastic housings.
And if that wasn’t enough, using nylon and other plastic and polymer composites makes cars quieter and more fuel-efficient. The average light vehicle in 2021 included more than 400 pounds of these materials, up from just 20 pounds in 1960.
Nor were carmakers the only industry using these materials. PA-12 also goes into solar panels, athletic shoes, ski boots, optical fibers, cable conduits, and flame-retardant insulation for copper wire. CDT is a key precursor for making many other chemicals, such as brominated flame retardants, fragrances, hot-melt adhesives, and corrosion inhibitors.
The March 2012 explosion and fire in Germany destroyed almost half the world’s production capacity for CDT. Worse, at the time of the explosion, CDT supplies were already tight due to its use in the booming solar panel industry.
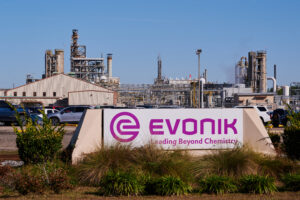
When a fire at Evonik Industries in 2012 destroyed capacity of a key chemical, automotive companies banded together as an industry to overcome the supply chain challenge.
Springing Into Action
For automotive companies, the potential impact of the Evonik fire was arguably similar to the potential impact of the 2011 Japanese earthquake. Every vehicle they made depended on PA-12 for a large number of parts, and the fire threatened a significant and prolonged disruption of car production.
When TI Automotive, a maker of fuel lines and brake lines, raised the alarm about the dire implications of the Evonik fire, the entire automotive industry sprang into action. The industry convened an emergency summit on April 17, 2012, in Troy, Michigan. The summit was moderated by a neutral third party, the Automotive Industry Action Group (AIAG). The AIAG is a volunteer-run, nonprofit organization that provides shared expertise, knowledge, and standards on quality, corporate responsibility, and supply chain management to about 4,000 member firms in the automotive industry.
Two hundred people attended the summit, representing eight automakers and 50 suppliers. Companies from all tiers of the affected sectors of the automotive supply chain came, including the big OEMs, their Tier 1 suppliers, component makers, polymer resin makers, and on down to chemical makers such as Evonik and BASF.
The participants had three objectives that required the collective expertise of the entire industry.
First, they wanted to understand and quantify the current state of global PA-12 inventories and production capacities throughout the automotive supply chain.
Second, they wanted to brainstorm options to strategically extend current PA-12 capacities and/or identify alternative materials or designs to offset projected capacity shortfalls.
Third, they wanted to identify and recruit the necessary industry resources required to technically vet, test, and approve the alternatives.
The group formed six committees to help quickly create action plans that would lessen any impact of shortages on component and vehicle production. Each committee tackled an assigned task, such as managing remaining inventories, boosting production at existing suppliers, identifying new firms to produce resins, and finding replacement materials.
The group hosted multiple technical follow-up meetings on this issue during the subsequent weeks.
This multifaceted collaboration was key to overcoming the supply challenge. Within one week of the meeting, the top OEMs had jointly drafted a plan to expedite their validation processes for alternative parts. Harmonized validation processes ensured that a supplier didn’t need to perform different validation processes for each customer OEM. Suppliers from other industries lent their capacity to automotive applications.
For example, Kansas-based Invista Inc., the maker of Stainmaster brand carpets, released its contractual claims on capacity for production of CDT so more could be allocated to the automotive industry. In the end, cars continued to roll off the line even though the Evonik factory was offline until December 2012.
Meet the Author
Dr. Yossi Sheffi is the Elisha Gray II professor of Engineering Systems at the Massachusetts Institute of Technology, where he serves as Director of the MIT Center for Transportation and Logistics (CTL). He is an expert in systems optimization, risk and resilience, and supply chain management, topics he researches and teaches at MIT and other leading business and engineering schools.
Outside academia, Professor Sheffi has consulted with numerous government agencies as well as leading manufacturing, retail, and transportation enterprises all over the world. He is also an active entrepreneur, having founded five successful companies, all acquired by larger enterprises.
Adapted from The Magic Conveyor Belt by Dr. Yossi Sheffi.
Available on Amazon, Apple Books and Google Play.