Construction Materials Management: Techniques, Software, and Benefits
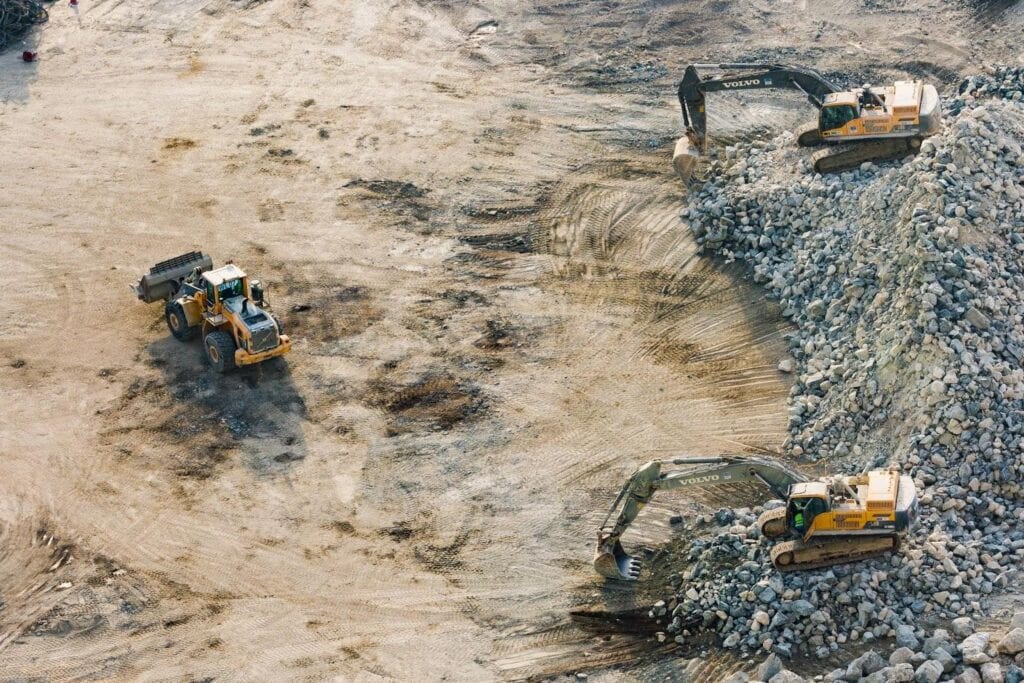
Construction materials management is pivotal in completing construction projects, ensuring that materials are available, of the right quality, and reasonably priced.
Every year, the construction industry faces significant challenges associated with material shortages, quality control issues, and logistical inefficiencies.
Implementing an efficient material management process is not just a cost-saving measure, but a strategy to improve project schedules, enhance quality, and minimize waste.
Effective Construction Material Management Techniques
Construction material management is integral in the building trade, and its effectiveness directly impacts project efficiency, costs, and completion timelines. This process encompasses a series of coordinated activities to plan, control, and optimize the procurement, handling, and use of materials during construction.
Effective material management is an art and science that aims to ensure the right materials are at the construction site at the right time, minimizing material waste and ensuring project schedules are met without inflation of costs.
The precise planning and execution of material management strategies are directly proportional to the overall project’s success. Poorly managed materials can lead to increased costs due to waste, delays resulting from material shortages, and a decline in productivity and quality of work.
Adopting a systematic and strategic approach to construction materials management is underscored by the need to control project costs, meet project schedules, and ensure quality construction outcomes, which are key deliverables every client expects.
Steps of Construction Materials Management Planning
The steps in planning construction materials management are multifaceted and aim to ensure efficiency and cost-effectiveness in construction projects.
Material Resource and Purchasing Planning
Accurate planning for material resources and purchasing is vital to construction materials management. It involves thoroughly analyzing the project requirements and specifications to determine the types, quantities, and timing of materials needed.
Comprehensive planning ensures that materials are procured reasonably and available when needed, preventing delays and cost overruns. For example, a construction project focused on building a residential complex requires a detailed material list, supplier negotiations, and a procurement schedule aligned with the project’s budget and timelines.
ROS–Required On-Site Scheduling for Construction Projects
Required On-Site (ROS) scheduling is another crucial component. It focuses on the timely delivery of materials to the construction site to align with the project’s phases, ensuring that work progresses without interruptions due to material shortages.
An effective ROS system minimizes storage costs, reduces material waste due to weather damage or theft, and enhances overall project efficiency.
In a scenario where a high-rise building is being erected, ROS scheduling ensures that materials like cement, steel rods, and concrete blocks are delivered in phases, corresponding with the construction schedule, thus maximizing productivity and reducing the need for extensive on-site storage.
AWP Advanced Work Packaging Preparedness
Advanced Work Packaging (AWP) is a planned, actionable process that aligns engineering, procurement, and construction activities.
The significance of AWP lies in its ability to improve project visibility, enhance team collaboration, and reduce inefficiencies, paving the way for a streamlined construction project.
For instance, on a commercial building project, implementing AWP ensures all stakeholders have a clear, unified view of tasks, materials, and timelines, minimizing delays and ensuring that material and human resources are effectively allocated to meet project schedules.
Sourcing Suppliers and Preparing Resources While Implementing Quality Control
Sourcing suppliers and preparing resources is pivotal in construction materials management, ensuring quality and cost-effectiveness. It entails vetting and selecting suppliers, negotiating terms, and establishing stringent quality control measures.
For example, in a bridge construction project, identifying suppliers who provide high-quality steel at competitive prices and ensuring the material meets industry standards can be the difference between the project’s success and failure.
Construction Organization and Storage Start-to-Finish Planning
Effective organization and storage planning from the project’s inception to completion are integral to minimizing waste and ensuring efficiency. This involves systematic storage, inventory control, and the timely retrieval of materials.
In a housing development project, a well-laid-out plan ensures that materials like bricks, tiles, and fixtures are stored, inventoried, and retrieved efficiently, reducing losses due to damage or misplacement and maintaining the construction schedule.
Engineering Implementation and Planning
This phase of construction materials management integrates engineering insights into the planning and execution stages. It ensures that the selected materials and construction methods align with engineering standards and project specifications.
In the case of constructing a hospital, for instance, this step ensures that materials and designs adhere to the required health and safety standards, enhancing the facility’s structural integrity and functionality.
Waste Reduction and Removal
Managing waste reduction and removal is crucial, focusing on minimizing material waste and the systematic disposal or recycling of waste. This is fundamental to cost savings and environmental conservation.
In urban development projects, an effective strategy ensures that waste – excess materials, debris, or used containers – is minimized and disposed of systematically, ensuring the site remains safe and efficient while contributing to environmental sustainability.
The Role of Successful Construction Material Managers
Construction material managers are pivotal in steering a construction project toward efficiency and success. Their expertise in construction materials management is not just a luxury but a necessity in the contemporary building trade. They bridge the gap between planning and execution, ensuring that the materials procurement and usage are optimized to meet project goals.
A construction material manager oversees the material management process, ensuring the right materials are sourced reasonably and available when needed. They are the custodians of quality control, ensuring that every piece of material used meets stringent quality standards, thus guaranteeing the safety and longevity of the constructed structures.
Their role in inventory management is also crucial. By ensuring accurate inventory levels and timely material deliveries, these professionals aid in minimizing delays, reducing storage costs, and avoiding the repercussions of material shortages or overstocking.
For instance, in a skyscraper construction project, the manager ensures that materials like steel, concrete, and glass are top quality and available in the right quantities and at the right time to avoid construction delays.
Furthermore, construction material managers are instrumental in waste management. Implementing efficient processes ensures that material waste is minimized, leading to cost savings and reduced environmental impact.
Their insight into effective material management strategies ensures that every step from sourcing to usage and waste disposal is optimized to achieve efficiency, cost savings, and sustainability.
Using Construction Material Management Software Applications
Technology plays a crucial role in streamlining operations in the modern construction landscape.
Construction material management software applications are invaluable tools that enhance efficiency, accuracy, and accountability in managing materials. These applications offer features that simplify inventory control, procurement, and usage tracking, among other essential functions.
For instance, Procore is a popular construction management software that offers a suite of tools tailored to enhance material management efficiency:
- Real-Time Inventory Tracking: These softwares provide live tracking of inventory levels, offering insights into available materials, those in use, and those that need to be ordered. This feature ensures that construction projects are on time due to material shortages.
- Order Management: This feature allows managers to place orders, track their status, and ensure they are received on time. It’s instrumental in ensuring that the project schedule is maintained.
- Quality Assurance: With this software, managers can ensure that the received materials meet the quality standards. It facilitates the inspection processes and ensures that only top-quality materials are utilized.
- Waste Management: The application aids in tracking and managing waste efficiently, ensuring that the job site remains clean, safe, and environmentally friendly.
- Reports and Analytics: The software offers detailed reports and analytics on material usage, waste, costs, and other vital metrics. These insights are crucial for decision-making and future planning.
Using Procore, a construction manager can ensure that the construction material management process is streamlined, efficient, and optimized for success. Every material ordered, received, used, or disposed of is tracked and accounted for, offering pivotal insights for cost management, efficiency, and accountability.
By implementing software applications like Procore, construction companies are equipped to handle complex projects with precision, ensuring that material-related issues do not become impediments to project’s timely and successful completion.
These applications are tools and essential partners that empower construction material managers to execute their roles with unprecedented efficiency and excellence.
Proper Construction Material Management Benefits
Construction materials management software, like Buildertrend, significantly enhances operational efficiency and accuracy in handling materials. This software offers multifaceted benefits including:
- Inventory Accuracy: Real-time tracking ensures accurate inventory data.
- Cost Management: Monitors expenditures, helping to stay within budget.
- Quality Assurance: Ensures materials meet required quality standards.
- Efficiency: Streamlines procurement, storage, and utilization processes.
FAQs
Find answers to some common questions about construction materials management below.
What are five major areas of materials management?
Procurement, storage, inventory control, quality assurance, and distribution are key areas in materials management.
What is the role of the material manager in the construction industry?
Material managers oversee procurement, storage, allocation, and waste management to ensure project efficiency and cost-effectiveness.
Effective Material Management
Construction materials management is pivotal for project efficiency, cost savings, and quality assurance in the building trade. Integrating software like Buildertrend ensures real-time inventory tracking, streamlined procurement, and effective waste management, aligning with project schedules and budget constraints while ensuring top-notch quality.