Hybrid Supply Chain: Definition, Strategies, and Advantages
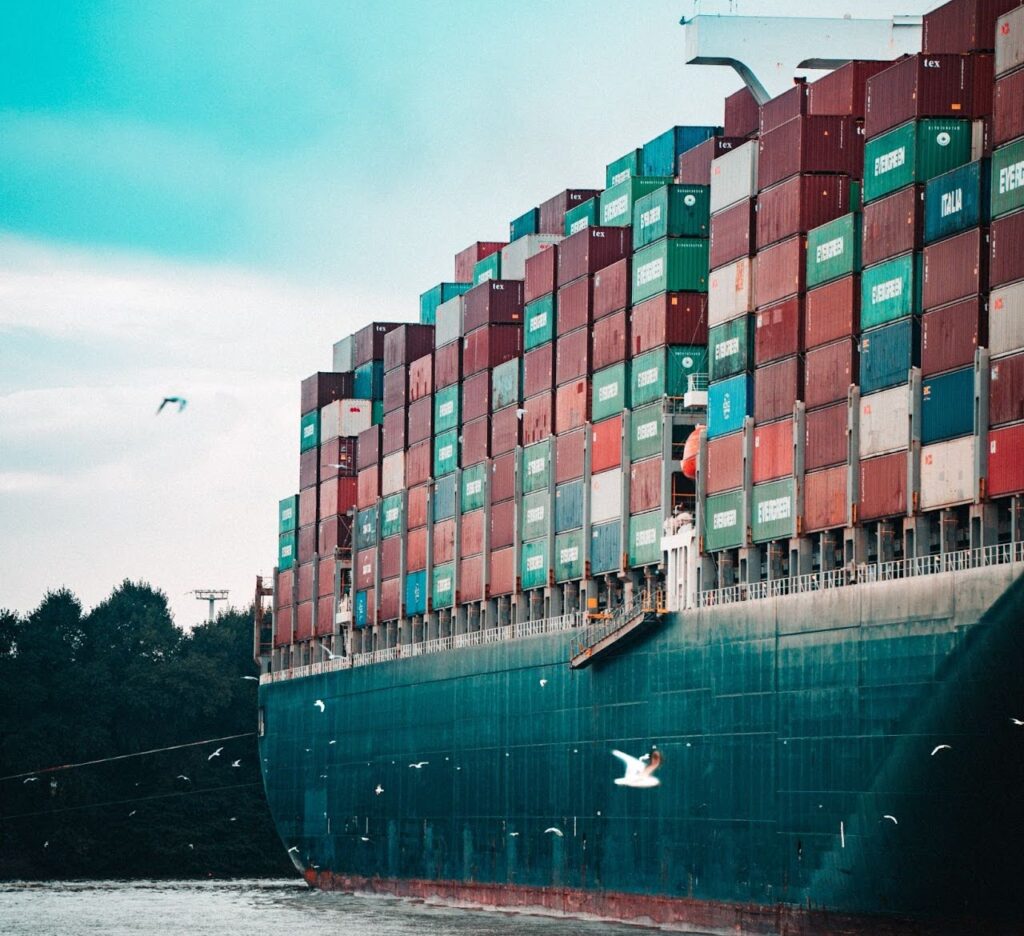
In an era where the pace of change is relentless, the concept of a hybrid supply chain has emerged as a beacon of adaptability and resilience in the business world.
The COVID-19 pandemic exposed vulnerabilities in traditional supply chains, leading to an increased interest in hybrid models.
According to a survey conducted by McKinsey & Company, 93% of supply chain executives have plans to increase the resilience of their supply chain, and for many, this includes adopting a more decentralized approach.
Incorporating this combined strategy allows businesses to meet actual demand with flexible production capacity, tailoring their approach to various distinct manufacturing processes and customer demand.
Understanding the Supply Chain Efficacy
The supply chain is the lifeline of any business, ensuring the seamless flow of products from creation to consumption.
Throughout its evolution, the drive for efficiency has shifted from the rigidity of traditional models to the adaptability of agile and efficiency of lean supply chain methodologies.
Now, the hybrid strategy is poised to define the future of supply chain management, merging lean characteristics for stable demand products with the agility required for less predictable markets, creating a flexible manufacturing system that can swiftly respond to changes.
Improving Supply Chain Through Hybrid Models
The hybrid supply chain represents a pivotal evolution in operations management, born out of necessity in industries where neither a purely lean strategy nor a fully agile strategy could meet the complex demands of the modern marketplace.
Industries such as pharmaceuticals and automotive have found a hybrid approach crucial, particularly as recent global events, like the COVID-19 pandemic, have revealed the vulnerabilities in singular supply chain models.
This combined strategy, implemented by entities from semiconductor manufacturers to fashion houses, demonstrates a shift towards more resilient and responsive business practices.
It has been particularly effective for companies with separate physical locations for different manufacturing partners, allowing for a more customized response to key customers and final customer orders.
Centralizing the Supply Chain
Centralizing the supply chain is a strategy employed by businesses to concentrate their logistics, decision-making, and operations in a singular, controlled environment.
This method is often seen in industries like consumer electronics, where companies like Apple centralize design and innovation while maintaining a global network of suppliers and manufacturers for production efficiency.
Advantages
Centralization within a hybrid supply chain can lead to more robust control over quality standards, uniformity in processes, and more effective monitoring of supply chain activities. It allows for better coordination, improved information flow, and can simplify the implementation of hybrid supply chain strategies.
Centralizing procurement, for instance, enables a company to negotiate from a position of strength, achieving better terms and lean characteristics across the supply chain, which can reduce costs and streamline manufacturing processes.
Methods to Cut Operating Expenses
Hybrid supply chains often adopt centralization to cut operating expenses by reducing duplicated efforts across various departments and geographies. Such an approach can lead to significant savings in logistics, as seen with global retailers who centralize their distribution model, resulting in less waste and lower costs throughout the supply chain.
Moreover, a centralized system can enhance demand forecasting, further aiding in reducing excess inventory and associated carrying costs.
Disadvantages
However, centralizing a hybrid supply chain can also introduce disadvantages, such as increased vulnerability to local disruptions affecting the entire supply chain. It may lead to longer lead times for supply chain partners located further from the central hub, and a loss of flexibility in responding to regional market variations.
The consolidation of operations may result in higher transportation costs and a potential disconnect from local markets, which can impact the ability to meet specific customer demands effectively.
Decentralizing the Supply Chain
Decentralizing the supply chain involves spreading various functions across multiple locations to enhance responsiveness and local relevance.
Fashion retailers like H&M employ decentralization to adapt quickly to changing fashion trends
in different markets.
Advantages
The advantages of a decentralized model within a hybrid supply chain are numerous. It brings agility and customization closer to the consumer base, making companies more responsive to local market demands and conditions.
This can be particularly beneficial in vast and diverse markets where consumer preferences may vary greatly by region. Decentralization enhances a company’s resilience to localized disruptions, such as natural disasters or political instability, by not concentrating all operations in a single area.
Disadvantages
However, decentralization carries its own set of challenges. The increased complexity of managing multiple facilities can lead to higher operational costs and potential inefficiencies. It may also result in a loss of centralized control and standardization, making it difficult to maintain consistent quality and processes across all locations.
Moreover, the redundancy of efforts and the potential to underutilize resources can negate some cost benefits typically associated with lean supply chain strategies.
Hybrid Supply Chain: Applying the Strategy
In a hybrid supply chain strategy, businesses can harness the advantages of both lean and agile methodologies to create a robust, responsive supply network.
This strategic fusion allows for a versatile framework that supports a broad spectrum of supply chain activities, from the manufacturing process to final product delivery, ensuring that each supply chain segment is optimized for both efficiency and flexibility.
Advantages
A hybrid supply chain strategy offers the flexibility of an agile supply chain with the efficiency of a lean supply chain. It supports companies in navigating the complex waters of the modern marketplace, where customer demand can fluctuate unpredictably, and production capacity must remain adaptable.
This combined approach can mitigate risks by adapting to customer needs while maintaining cost-effectiveness, leading to improved customer satisfaction and service levels.
Disadvantages
The primary disadvantages include the complexity of managing two different supply chain strategies and the potential for internal conflict between the lean and agile approaches.
Balancing these can be challenging and require sophisticated supply chain management tools and processes. For example, the lean aspect of the strategy, focused on minimizing costs, must be carefully aligned with the agile side, which may require investment in flexible manufacturing capabilities.
Maintaining inventory at multiple locations to ensure agility contradicts lean supply chain goals of reducing inventory levels. Therefore, a hybrid supply chain requires a nuanced approach to operations management, ensuring that the benefits of both lean and agile methods are realized without compromising overall supply chain efficacy.
FAQs
Quickly grasp the nuances of a hybrid supply chain with these frequently asked questions.
What is an example of a company using a hybrid strategy in its supply chain?
Dell uses a hybrid strategy, combining build-to-order and build-to-stock in its supply chain.
What is the opposite of an agile supply chain?
The opposite of an agile supply chain is a rigid or lean-focused supply chain.
Is Zara’s supply chain lean or agile?
Zara‘s supply chain is primarily agile, with some lean aspects incorporated.
What is lean & agile supply chain?
A lean & agile supply chain combines efficiency and flexibility to meet variable demand.
The Bottom Line of Supply Chains without Hybrids
Supply chains operating without the versatility of a hybrid supply chain often need help to keep pace with the dynamic demands of the competitive global economy.
The hybrid approach taps into the strengths of both lean and agile supply chain methods, allowing for flexible production capacity and thin supply chain focuses that are crucial for businesses to meet the actual demand and achieve competitive advantage.