Order Picking: Definition, Methods, and Advantages
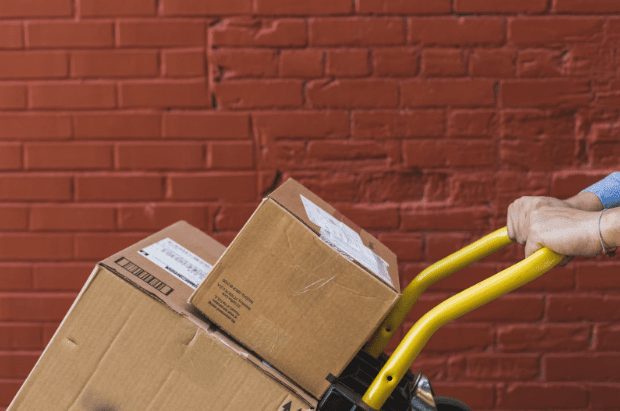
Order picking is the process of products being retrieved from warehouse inventory to fulfill orders by customers. This article will describe order picking, how it works, and ways order picking processes can improve supply chain and business results.
What is Order Picking?
Order picking, or the warehouse picking process, refers to selecting items from a warehouse’s stock to fulfill your company’s customers’ orders. It’s hard work that requires speed and precision. Efficiency is crucial to the order-picking process since the time it takes to prepare an order significantly impacts the timeliness of its shipment.
Order pickers spend most of their time searching through a specific warehouse for the products to fulfill customer orders. Forwarding-thinking businesses can implement methods to reduce the distance and time required for order pickers to find the products that they need to fulfill customer requests.
The reason order picking is essential is that it’s a crucial step in delivering client orders. Customer satisfaction may be impacted by how quickly and accurately orders are picked and packed for shipment. As a result, streamlining this procedure is crucial for promptly and adequately fulfilling client orders.
Types of Order-Picking Methods
There are a lot of order-picking methods that can be used in this process. Here are some of the methods used frequently today.
Single Order Picking
The single-order picking method is commonly used. Here, order pickers work on a single order at a time. It’s not uncommon for them to travel across the warehouse in search of the same product. Due to how long it takes to manually go from one point in a large warehouse to others – some miles apart – this approach is slow and typically reserved for less busy businesses or warehouses. However, concentrating on a single order at a time typically results in a high degree of accuracy, so this system continues to be widely used.
Batch Picking
Batch order picking is also called multi-order picking, and as the name suggests, it involves multiple orders being picked simultaneously, with each picker focusing on a single item category. Any company regularly placing repeated orders for the same SKU would find this method useful. It is also effective for companies with only a few SKUs.
Using this method, the pickers only need to go to the storage area where an item is kept once, instead of traveling to various locations in a warehouse making order picking more efficient. That is one of the reasons that batch picking is commonly used.
Cluster Picking
Order pickers can use the cluster-picking technique to complete numerous orders at once. However, rather than focusing on picking multiple identical SKUs for several orders, pickers choose a wide range of goods for each order.
There are several methods for cluster picking including using vertical lift modules and carousels. However, the most common practice is for an order picker to push a cart full of containers from one location to another. Picking carts and other forms of collaborative mobile robots assist pickers in staying organized and minimizing errors while fulfilling orders.
The amount of time that order pickers save on traveling using this method is less than the time saved with the batch order picking method, but it’s still significant. A cluster picker only has to visit a zone once for each cluster they are processing.
Wave Picking
The warehouse gets split up into sections when using the wave order picking method. For efficiency, pickers stay inside their designated areas and do their tasks simultaneously. Because of this approach, wave order selection may be a good option for organizations that wish to speed up their order selection process. This method may be beneficial for companies whose orders often include various products.
Pick and Pass
With the pick-and-pass process, the storage facility is partitioned into sections, and warehouse workers are allotted to certain zones. To expedite the fulfillment of orders, associates may often make several SKU selections from the same zone’s bins, totes, or containers before passing them on to the next zone. Zone picking is not the same as the pick-and-pass process. Order pickers may also do zone picking without moving bins or containers between zones.
Zone Picking
If your warehouse is divided into sections, then zone picking is a great picking solution for your business. Orders from different parts of the warehouse are distributed to pickers allocated to their respective zones. Warehouses that often receive high-volume orders (orders containing a significant number of products) benefit most from zone picking.
Sorting System
In the sorting system method, conveyor belts and other automated equipment do the sorting. With this setup, pickers use a conveyor belt to transport products from storage to the workers who will fulfill customer orders. This technology is quite effective since it enables companies to automate several aspects of the order selection process.
Pick to Box
A conveyor belt is used in the pick-to-box method. When using this technique, a picker sets the box down on a moving conveyor belt. As the box travels between zones, pickers fill it with the necessary contents. This technique may assist firms in dealing with high order quantities and reduce congestion caused by order pickers.
Picker to Part
The picker-to-component system is a good order-picking strategy if you want to streamline your order-selecting procedure. Typically, forklifts are used to move goods throughout the material handling section, which is built up in warehouses utilizing this technique. Order pickers use the system’s picking area to assemble orders for shipments.
Part to Picker
When fulfilling an order using the picker-to-part technique (also known as picker-to-goods), the picker searches the warehouse to locate the specific products that have been requested. Single-order picking, batch picking, and wave picking are just some methods available to teams that need to fulfill orders quickly. This technique provides for a more flexible workflow, but it also causes more time spent traveling.
Piece Picking
Order pickers do component picking by fulfilling orders individually. That way, the picker isn’t juggling many orders at the same time, and selecting mistakes should be minimized. Piece picking may be time-consuming due to the picker having to travel the length of the warehouse many times to pick up each order.
Piece picking is most efficient for low-volume businesses handling a limited number of orders each day. Third-party logistics warehouses sometimes employ piece picking to effectively complete a rush order or push through the last orders towards the end of the work day. Still, most third-party logistics companies don’t use piece-picking as their main strategy.
Pallet Picking
One method of storing goods in a warehouse is on wooden platforms called pallets. A pallet may carry a single big item or several little items, depending on its size. Thus, pallet picking is used when a full pallet of goods gets picked and transported to the packing area.
Case Picking
When using the case-picking method, products are selected from several storage options including pallet positions, carton flow racks, shelving, and in whole cases or cartons. Faster-moving items are often selected from pallet placements for most processes.
Products that move at a medium to slow pace are often selected from a flow of cartons. Products with a low rate of turnover are taken off stationary shelves. Product is often picked onto a pallet flow, trolley, or conveyor by personnel. Orders are sorted and packed in a certain order as the picker makes its way through the warehouse aisles.
Discrete Picking
Discrete order picking is a common strategy used in warehouses because of its simplicity and straightforward implementation. Individual goods are selected by pickers until the order is complete.
This approach works well for warehouses that get fewer orders and stock fewer SKUs. With this method, it’s simple to monitor the precision of the order pickers, and the turnaround time for fulfilling orders is much reduced. Discrete picking is a labor-intensive and inefficient method for warehouses that deal with higher-volume or more complicated orders due to the time spent traveling between picking locations.
Combined Order Picking Methods
If none of these strategies seem right for you, you can try combining two of the aforementioned methods. Here is a quick overview of the most popular combination order-picking methods.
Zone-Batch
Order pickers are given a zone to work in, like in conventional zone picking, but they are also instructed to do batch picking inside their zone. The scheduling window for zone-batch picking is the same as that for zone-picking and batch-picking.
Zone-Wave
In Zone-Wave Picking, each picker is responsible for picking all SKUs for all orders stocked in their assigned zone within their shift’s allotted time slot.
Zone-Batch-Wave Picking
Zone-Batch-Wave Picking is the most intricate approach to combining many order-gathering techniques. It is the responsibility of each picker to select all products for orders that come from their designated zone. Moreover, the picker picks all the products simultaneously, and each shift has many available time slots for scheduling.
Automated Picking Processes
In order to improve how efficient human order pickers are, robotic and semi-robotic technologies are being used to automate warehouse picking. There is a large variety of automated warehouse-picking alternatives available. However, the most effective automation technologies are those that fit within your current warehouse procedures with little disruption and can be used collaboratively with teams.
Integrating automated warehouse picking with your current warehouse management system can facilitate precise picking and packaging benefitting your company.. It doesn’t matter what industry you’re in. Your business will benefit from automation.
Pick-to-Light
In the pick-to-light picking process, barcode scanners and pick-to-light LEDs installed at strategic intervals throughout the warehouse’s racks and shelves are necessary for this order fulfillment system to function properly.
The first step for a picker is to scan the barcode on the shipping box that will house the products for that order. If you scan a shipping box, the LEDs corresponding to the goods in your purchase will light up. Thus, the picker needs to just follow the light until their order is complete. Pick-to-light technology shortens the amount of time required for the picking process and saves money on labor expenses.
A pick-to-light method is a good option if you’re trying to improve your picking accuracy and reduce the time it takes to fulfill orders.
Voice Picking
Voice-picking solutions are digital, hands-free technologies that guide your warehouse workers in charge of order fulfillment to specified places inside a warehouse and inform them which SKU to choose to complete client orders with simple, easy-to-understand voice prompts.
It’s increasingly common warehouse automation that helps pickers concentrate on their work by freeing their hands and eyes from other things like reading labels and pressing buttons. It’s a great option for companies looking to improve warehouse productivity.
Mobile Scanner Picking
With the help of mobile scanning software, warehouses can instantly confirm orders and monitor and allocate pick tasks, all from a mobile smartphone or scanner. As a result, manual picking mistakes are eliminated, and worker output is increased via mobile scanning and order verification automation. As a result, your warehouse can function with greater order accuracy.
Mobile scanning software is ideal for businesses looking to improve order accuracy and customer satisfaction.
How to Choose an Order-Picking System
How well your business runs may largely depend on the order-picking technique you use in your warehouse. Your order-picking strategy also plays a role in keeping the space organized and safe for everyone who works there.
Additionally, selecting and using the optimal order-picking technique for your company may boost customer satisfaction and experiences, which is crucial to maintaining existing customers.
Some factors that you need to consider when choosing an order-picking process are:
- The times that your order pickers will work.
- The safety of your workers
- The number of workers that you have
- The type of products that your business sells
- The size of your products and the number of products your customers typically order
- How often do your customers order from you?
- You should also have a few goals in mind when choosing an effective order-picking strategy.
Minimizing The Amount Of Time That Your Workers Have To Travel
One of the major areas of inefficiency in a warehouse is travel time, or the time employees spend moving throughout the facility to get products. Half or more of a worker’s shift may be spent just moving from one item to the next.
If you have to pick something up from a few feet away and then go back to where you left it, it’s easy to spend most of an 8-hour shift being unproductive. Arrange the warehouse in a way that minimizes the need for movement and provides efficient picking routes.
Make sure commonly requested items are placed near one another and stock those that move quickly near the packaging area. Check in with employees regularly to see what slows them down as they go across the warehouse.
Making Your Workplace As Safe As Possible
Workplace accidents may be avoided by prioritizing warehouse safety. Occupational health and safety regulations, such as forklift safety or safety gear requirements, tend to get more attention, but ergonomics is something you need to consider too. This can play a major role in reducing accidents in the warehouse.
Preventable strains and injuries may occur from doing the same actions repeatedly, particularly when dealing with large materials. Use trolleys and conveyer belts wherever you can, and make sure everything is placed at a safe height. For the best results, allow workers to pause to stretch and relax during their shifts to limit fatigue and potential errors.
Improving Picking Accuracy
Mistakes may be made by choosing the wrong products, leaving out necessary components, or inserting an incorrect number of items. If you send the wrong products, your customers might return them, or they may be put back on the shelves.
If the packing crew is given an incorrect number of a particular SKU, your order picker will need to make another trip through the warehouse to either get the missing items or send back the surplus.
Technology like as voice picking and pick-to-light systems may help reduce human mistakes, which is always a possibility. It is important to keep track of error occurrences and investigate them thoroughly to determine root causes. Many mistakes result from inefficient procedures, broken machinery, or an unreliable logistics provider, all factors beyond the control of your employees.
Making The Most Of The Available Space
If products are scattered about the workplace, employees will spend time looking for them. Narrow aisles may impede the movement of forklifts and other material-handling equipment.
Congestion may develop in poorly designed spaces that don’t facilitate the free movement of people and goods.
A well-organized warehouse makes better use of available square footage and facilitates faster order fulfillment. When there is a logical flow to the layout of a workplace and items are properly shelved and sorted, productivity soars.
Advantages of Using an Order Picking System
These are some of the many benefits of using an order-picking system.
Exceed Customer Satisfaction
The efficiency of warehouse picking may directly impact customer satisfaction because it can impact whether or not a shipment arrives complete or with erroneous or missing products. Customer satisfaction is impacted if an order is not received at the time promised or if the product is damaged.
Boost Efficiency
A streamlined warehouse picking system improves efficiency and accuracy for your warehouse staff. Picking efficiency and accuracy may be increased by providing workers with optimal routes that include validations and images to verify they are retrieving the correct items from the order.
Improve Cost-Effectiveness
Operating a warehouse efficiently may require multiple software solutions like Warehouse Management System (WMS) technology. Your WMS may generate an automatic picking list, which will assist your pickers as they fulfill client orders.
Choosing a warehouse order picking system that can assign many orders that are close together to the same picker can improve accuracy and efficiency.
Final Thoughts
There are various order picking methods to choose from for different types of businesses. Taking the time to select an order picking process that meets your needs will help improve results and efficiency.