Reducing the Impact of Global Events
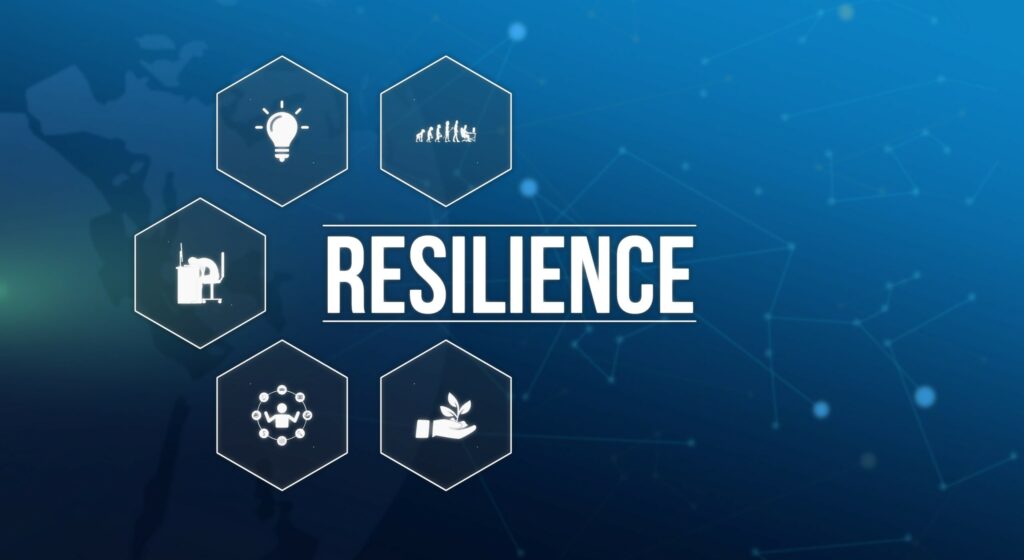
The global supply chain became even more connected in 2022. The U.S. Commerce Department reported record exports to 73 countries last year, and record imports from 90 nations. But the supply chain remained highly fragile and became a bigger responsibility to manage.
Events like Russia’s invasion of Ukraine and a rise in canceled sailings had rippling effects on supply chain resiliency in the United States and throughout the world. Nearly 72% of businesses were hampered in some fashion by global events, finds the 2022 Supply Chain Disruptions Study. Now in 2023, tragic earthquakes in Turkey and Syria are creating the same problems.
To hedge against global setbacks, consider product sourcing diversification and nearshoring. Both strategies can reduce risk by ensuring access to the necessary materials and labor resources.
Let’s take a deeper look at how both strategies not only reduce risk, but also optimize business efficiencies and create resiliency.
Product sourcing diversification. Businesses gravitate toward product sourcing diversification because it’s an effective way to spread their risk. By having multiple suppliers available for the same product, operations can fall back on a different supplier should one be impacted by unforeseen disruptions.
This strategy grew popular during the Trump administration because of tariffs placed on goods imported from China. Many companies were forced to rethink their dependence on trade with China and diversified elsewhere in Asia.
Businesses have looked specifically at India and Vietnam because they can offer the needed products at a cheaper price and lesser risk.
Spreading the risk is a key pillar to supply chain stability. The ability to still acquire necessary products, despite difficulties from events beyond their control, allows businesses to remain stable and trustworthy to their clientele.
Nearshoring. Moving supply chain operations to a country closer to the import destination, which still gives businesses the advantage of cost savings associated with offshore production, is a strategy that’s picking up steam. In an Accenture survey, 94% of companies said they are directly investing in nearshoring or onshoring, and 85% want their factories and material sources to be in the same hemisphere.
It’s easy to see why. Nearshoring not only spreads the risk, but also shortens lead times to result in faster cash-to-cash cycles, reduces inventory carrying costs, and facilitates more efficient visits by quality assurance and purchasing staff.
Nearshoring also helps businesses shift to a more practical “just in case” inventory management strategy, instead of the traditional “just in time” approach to foster better overall resiliency.
Most importantly, reaction time in a global setback is much faster with nearshoring. Being in the same time zone allows for easy communication and collaboration during a crisis.
Mexico is particularly attractive because it offers many more logistics options for moving goods. It’s not limited to ocean and air freight, which can prove to be a big difference during a global setback. Mexico also offers tariff stability due to the U.S., Mexico, Canada Agreement (USMCA).
Supply chain volatility requires businesses to do everything they can on the back end to minimize risk. Product sourcing diversification and nearshoring achieve those objectives and create more efficiencies.
By adopting these strategies, businesses reap the benefits of cost savings associated with overseas production and hedge against global setbacks or unexpected supply chain disruption.n